INNOVATION CULTURE
We have a culture of innovation. For more than 30 years we have been researching new technologies that we apply in the development of products, providing solutions that significantly improve the daily work of professionals around the world.
INNOVATION
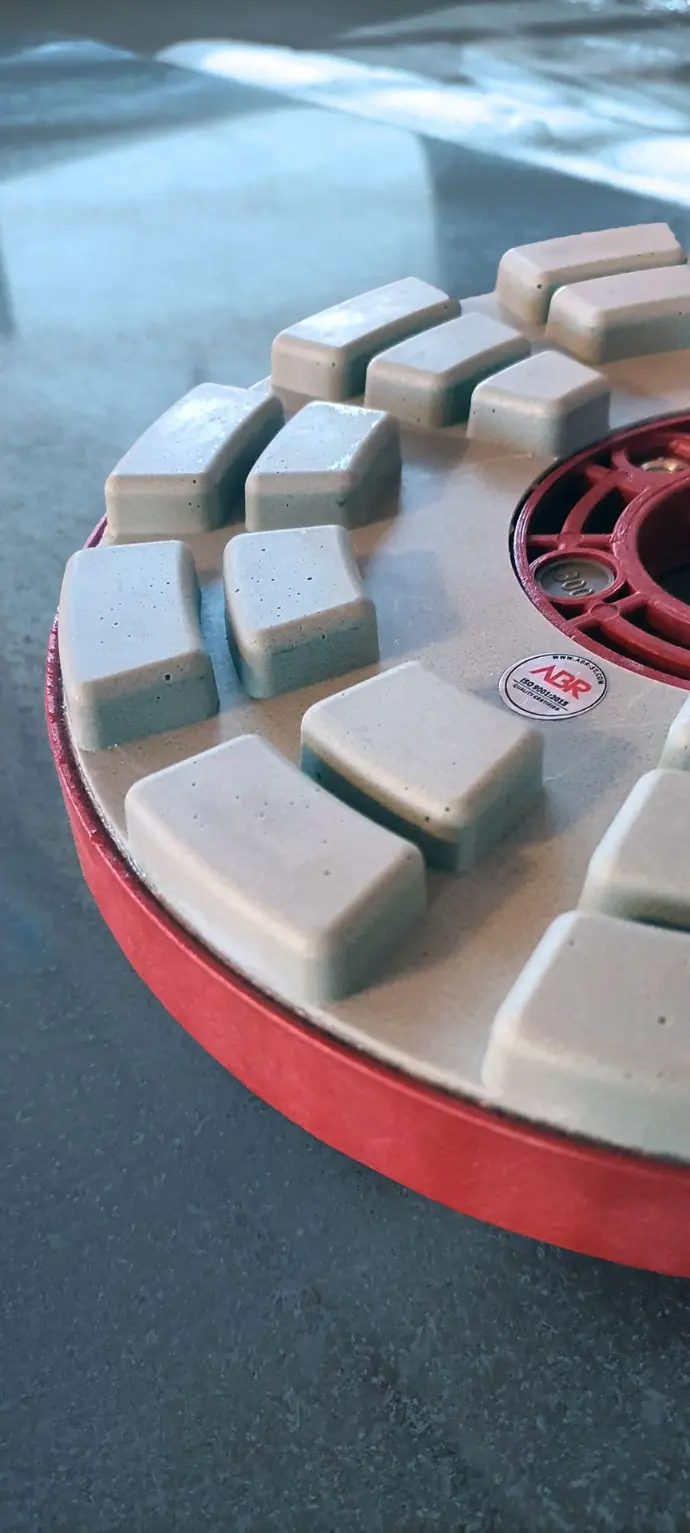
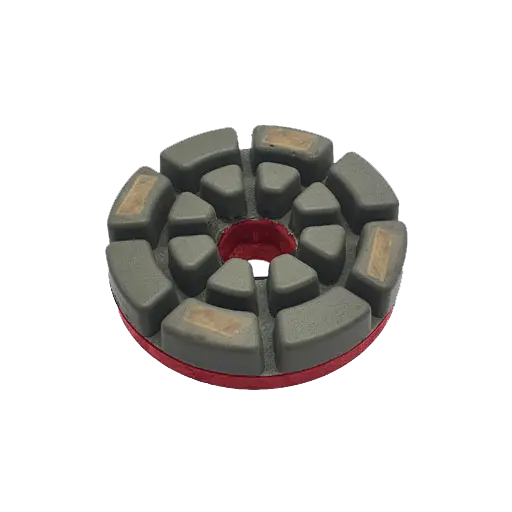
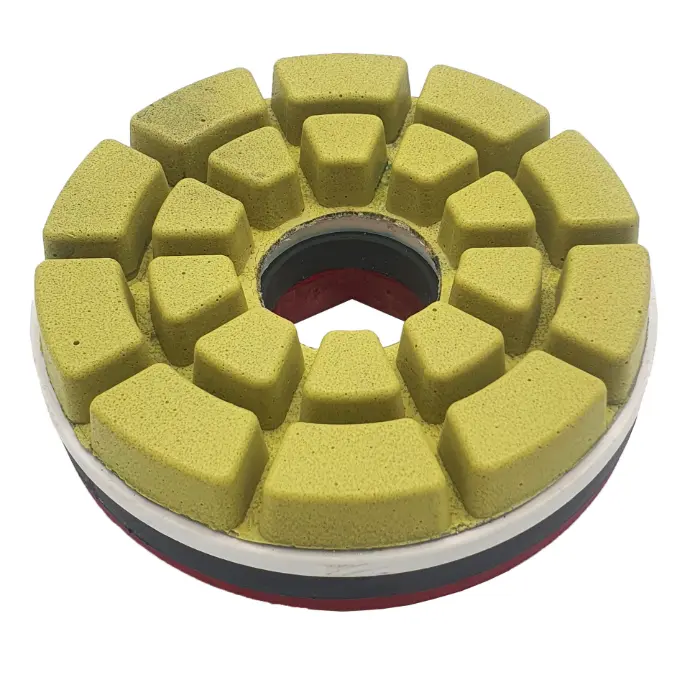
Latest generation diamond technology developed to achieve products with a very low cost but with maximum performance and quality.
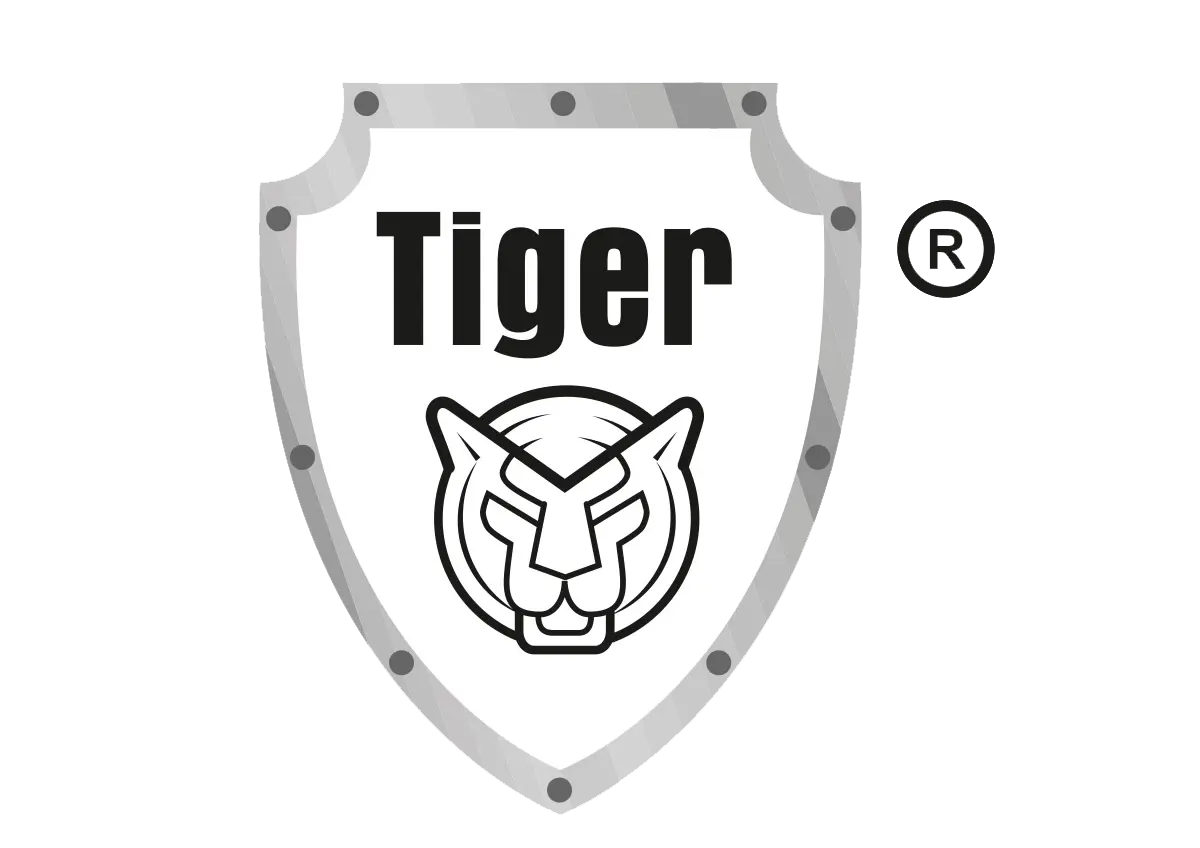
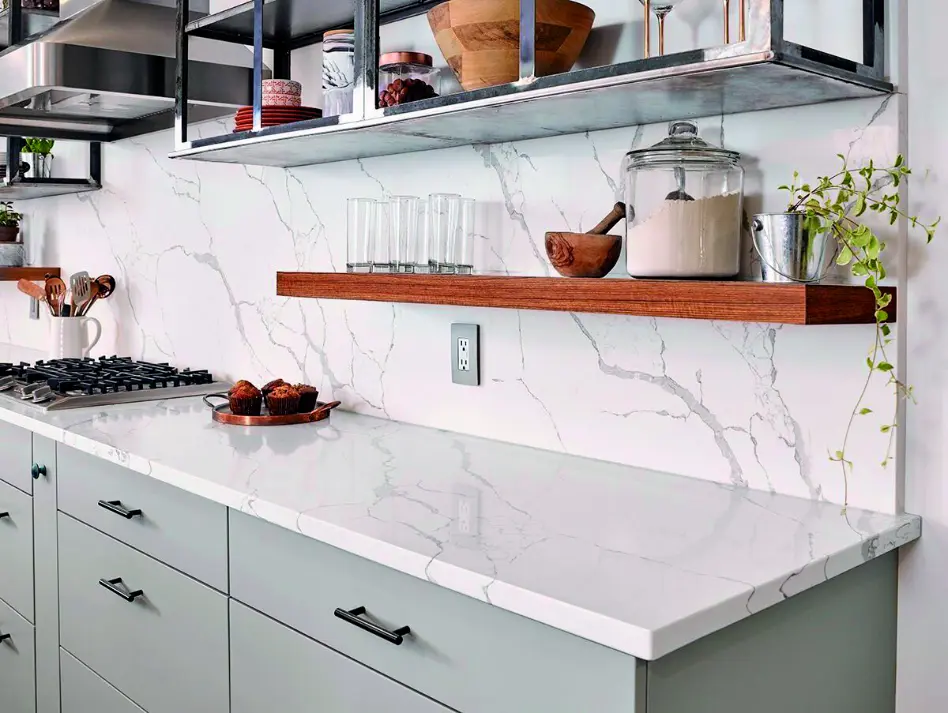
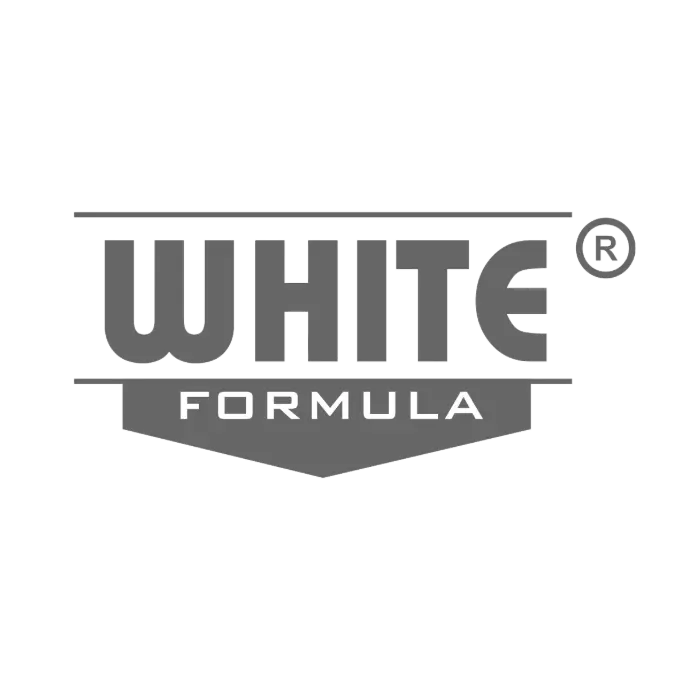
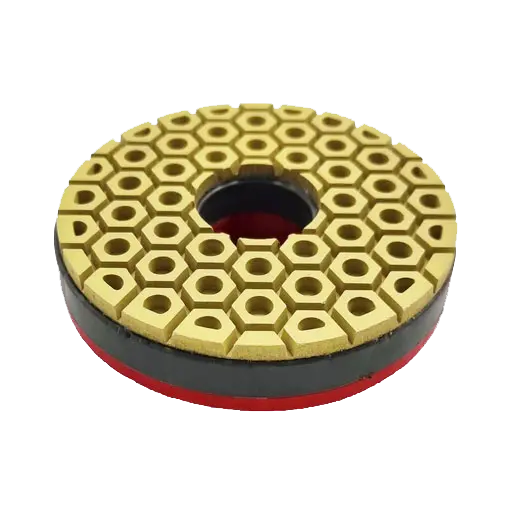
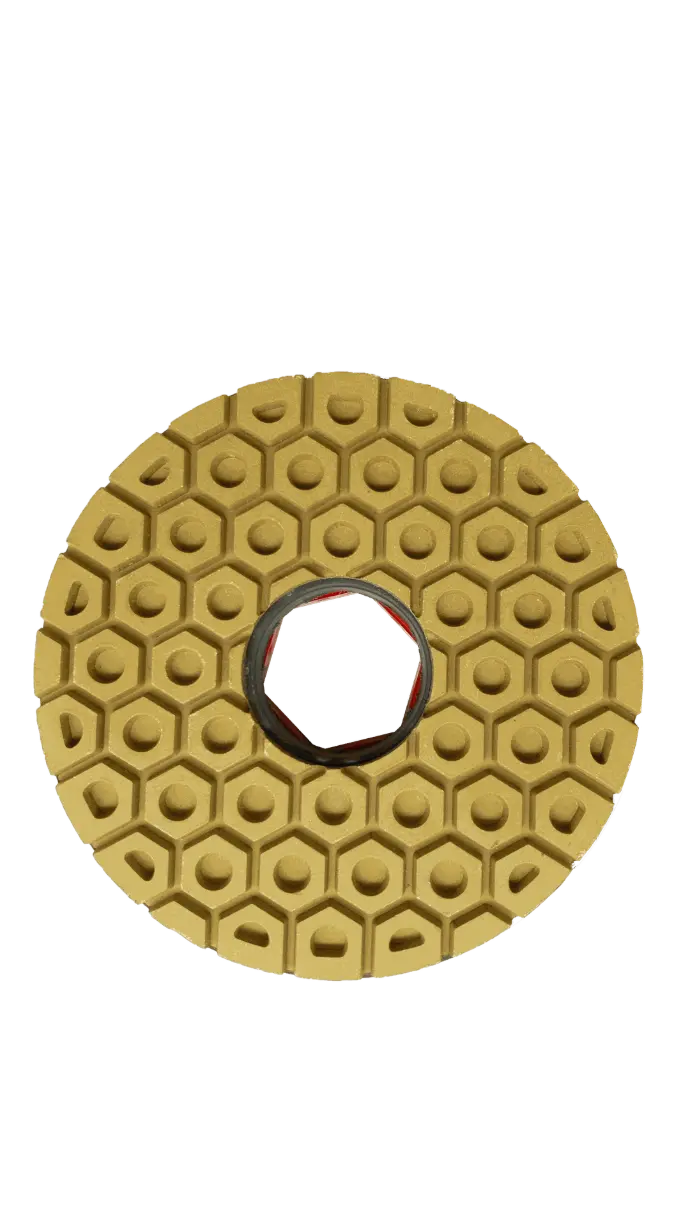
Revolutionary diamond-coated formula with no pigmented fillers. Eliminates the risk of color transfer, achieving a perfect polish on any surface.
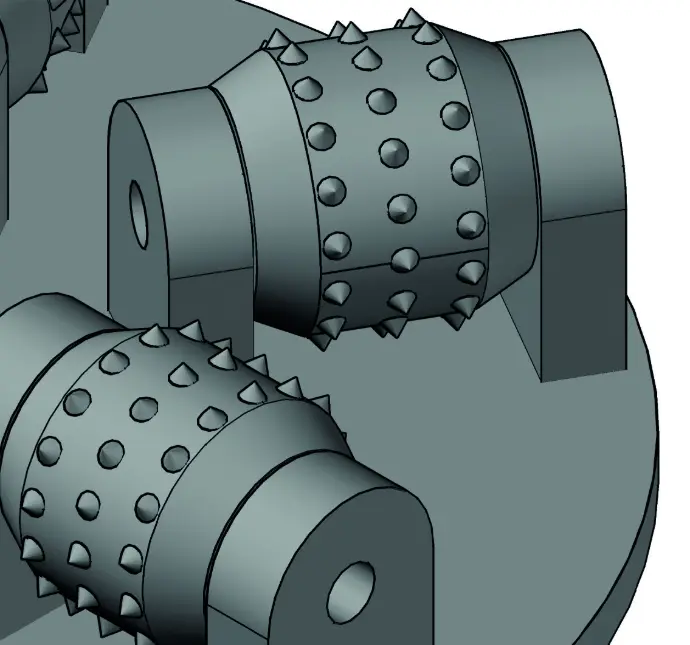

Innovative hot-press vulcanising system used in the manufacture of technical tools. It outperforms the traditional construction system, avoiding defective welds and manufacturing failures.
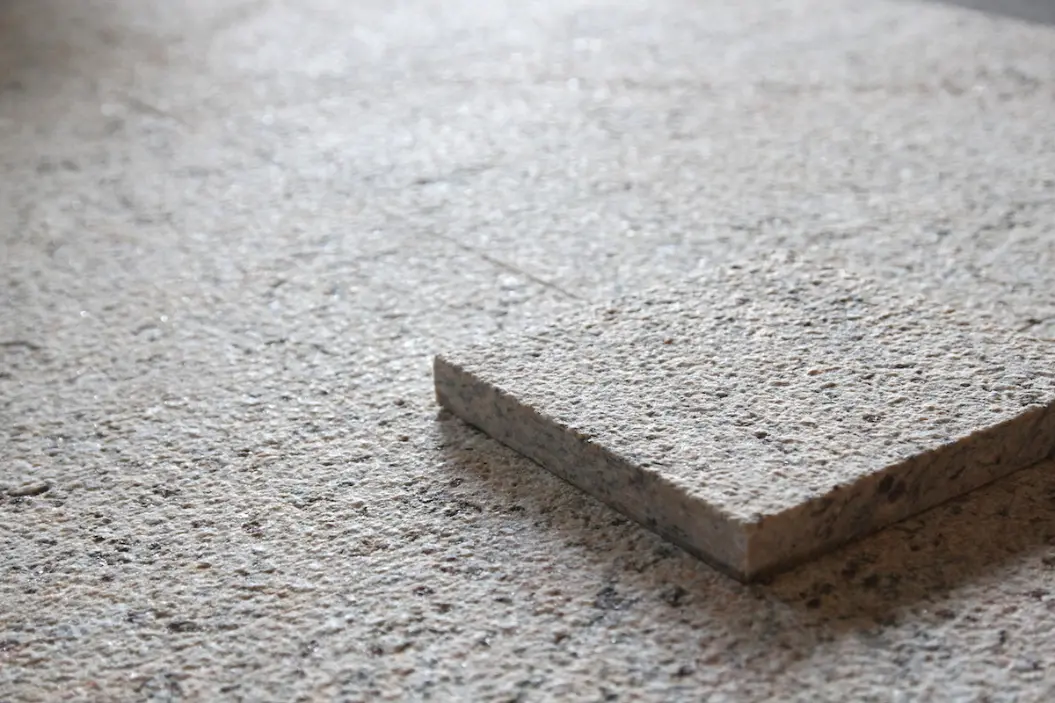

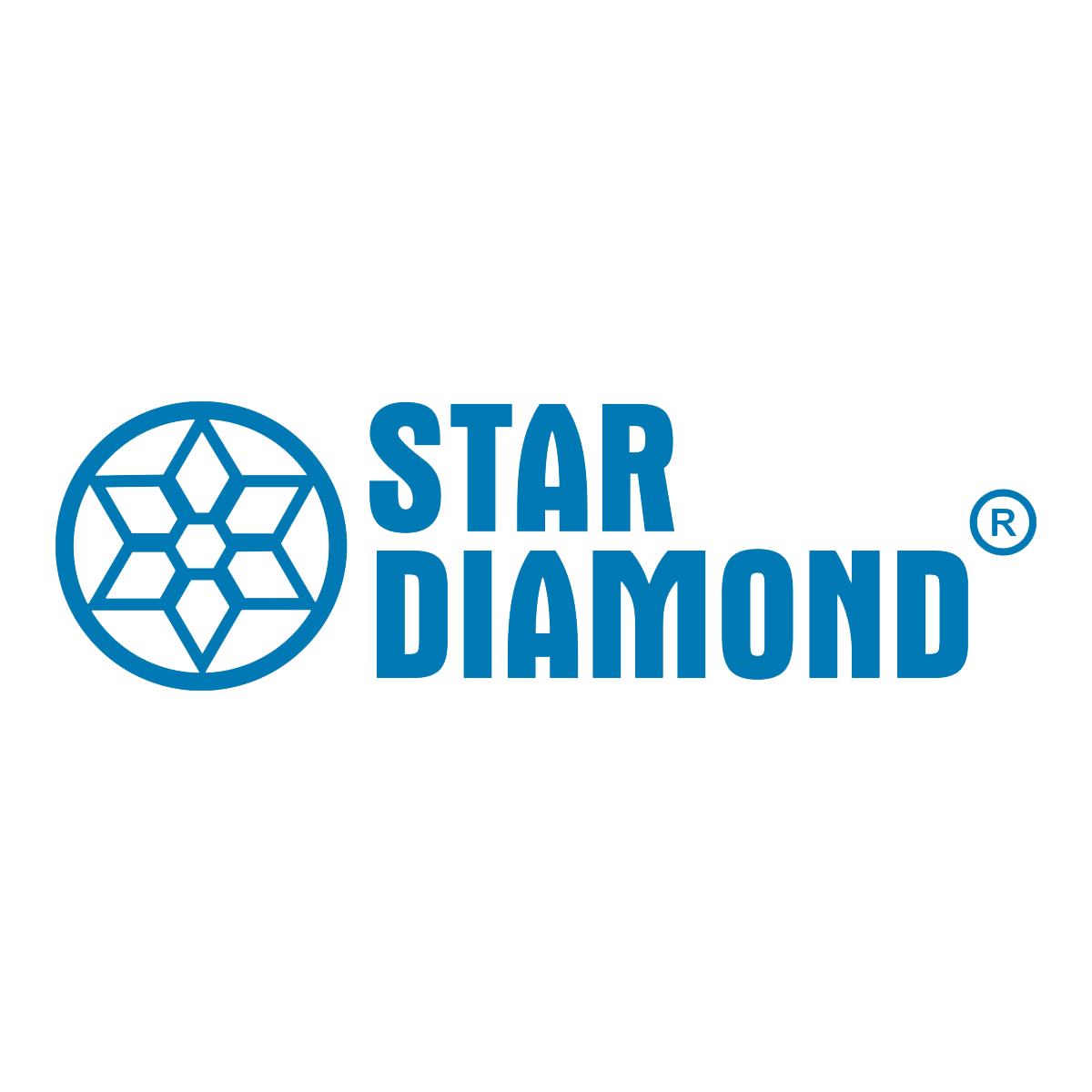
186 / 5.000 Multi-Channel System designed exclusively for excellent cooling. Keeps the tool cool and in optimal working condition throughout its entire lifespan.
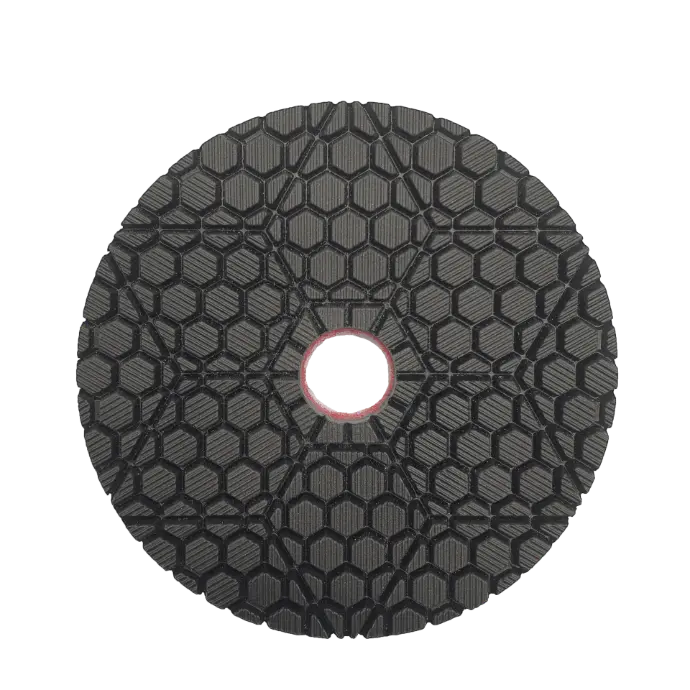
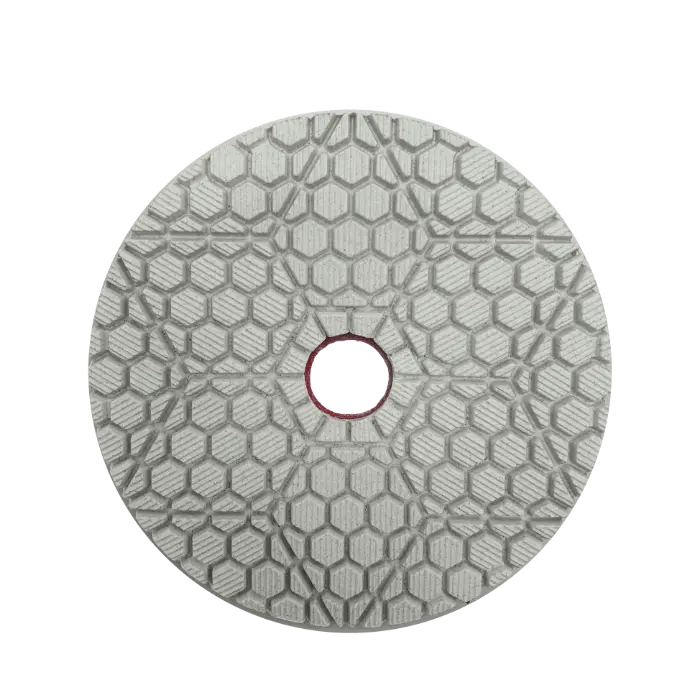
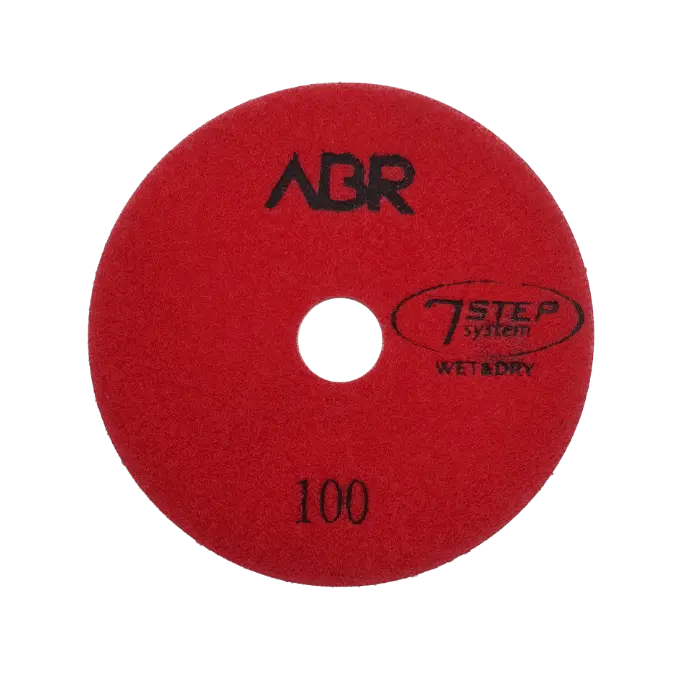
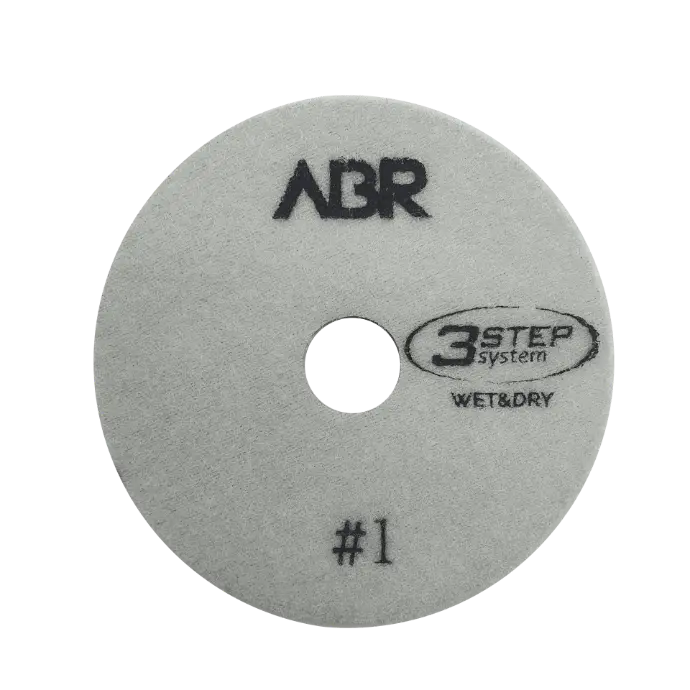
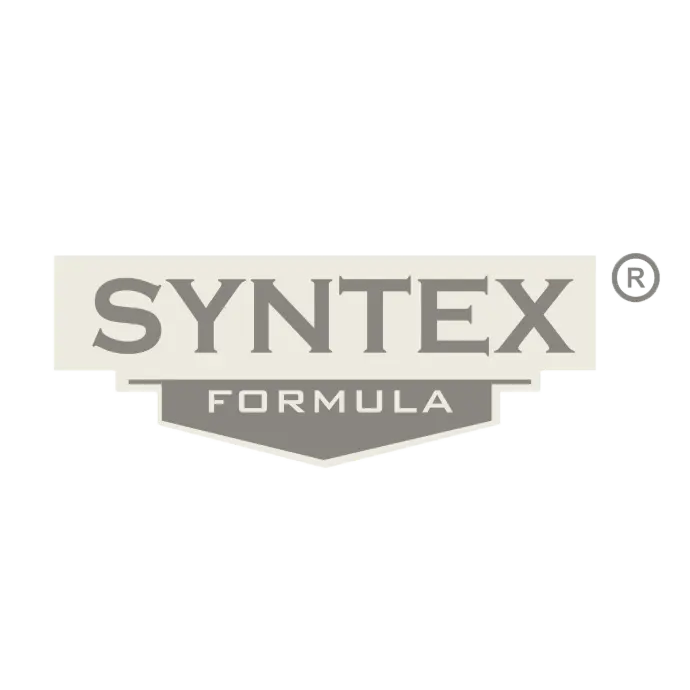
The combination of minerals with magnesium oxide, bonded using synthetic resins in a consolidated production process, results in highly economical, high-performance abrasive products that are stable over time.
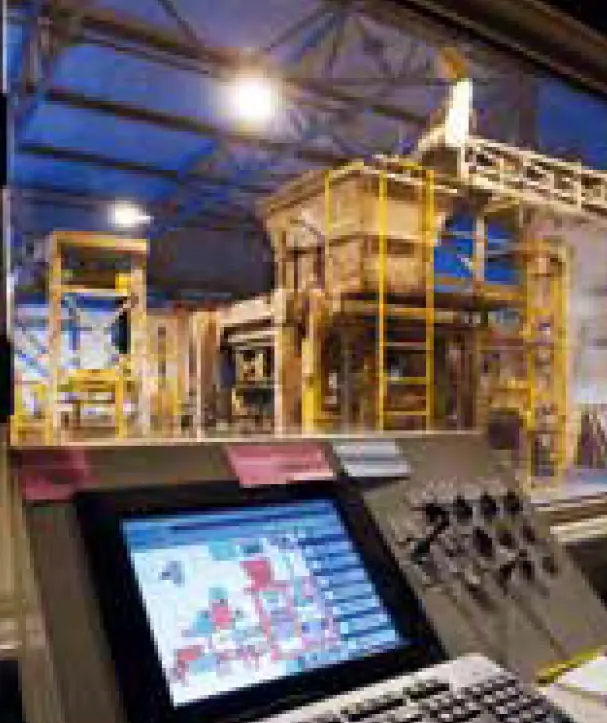
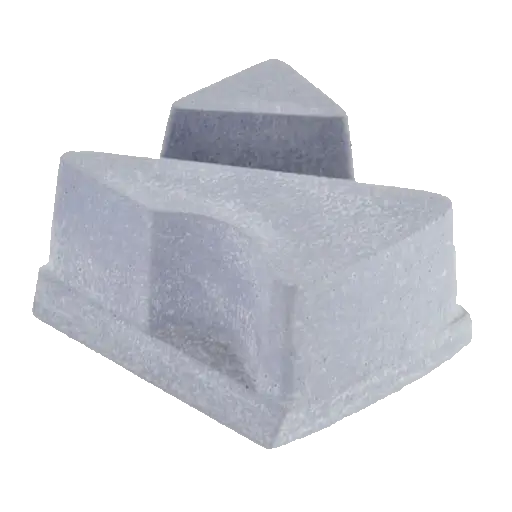
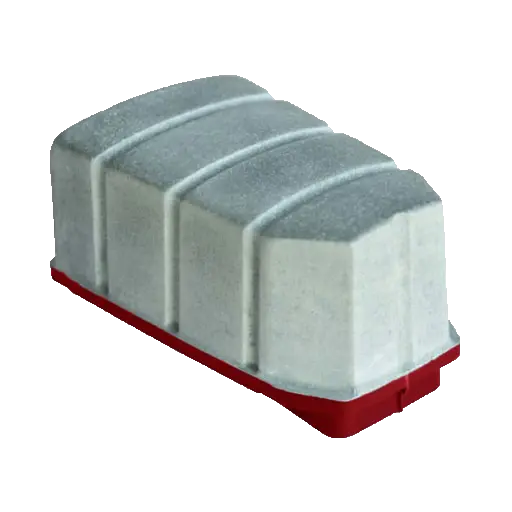
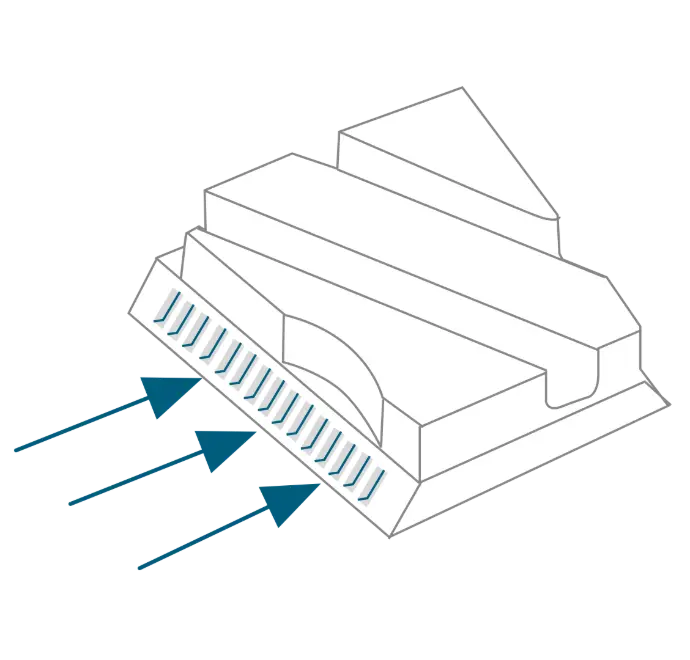
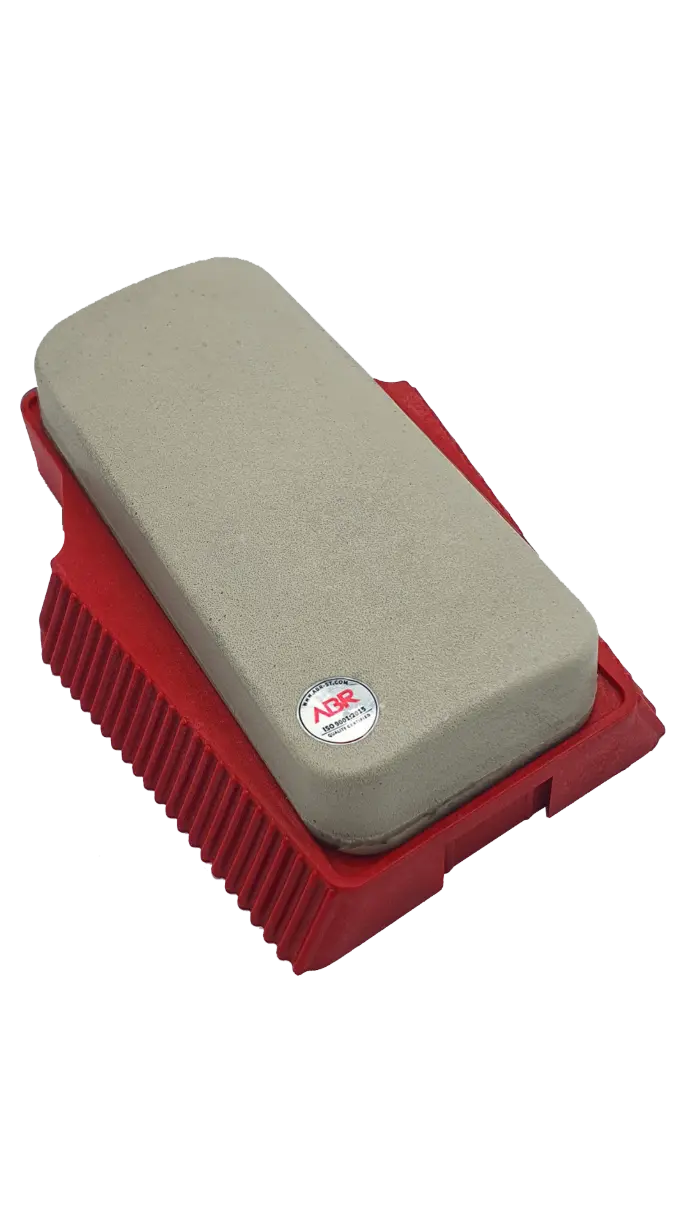
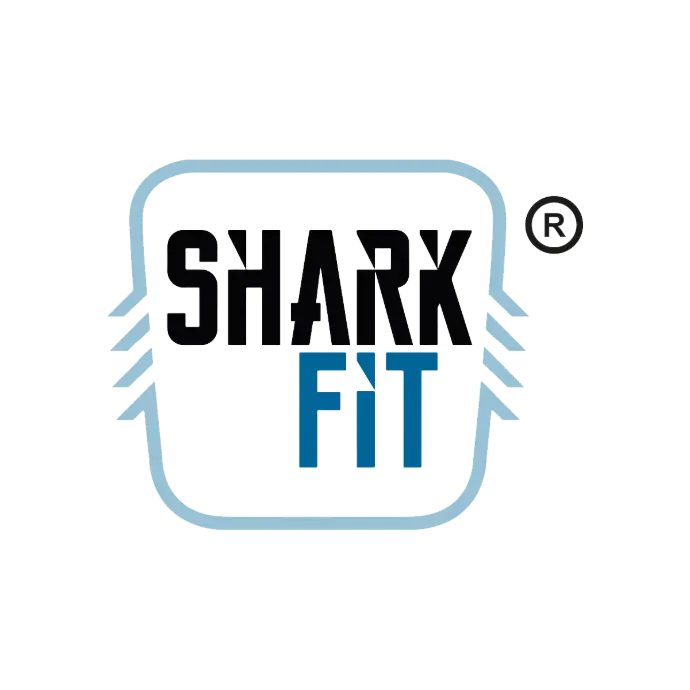
Small incisions in the supports ensure perfect fitting of the tool to its attachment.
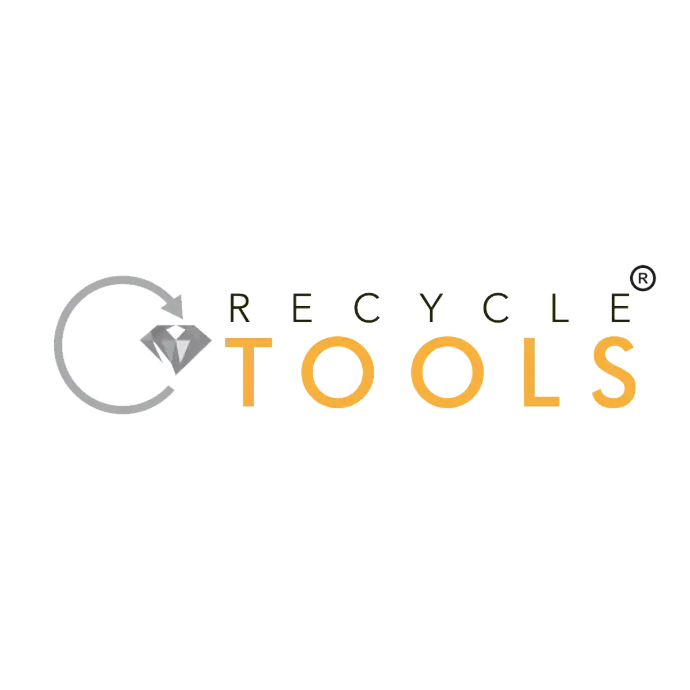

A process for restoring and reconditioning worn tools, maximizing resources and achieving extraordinary savings.
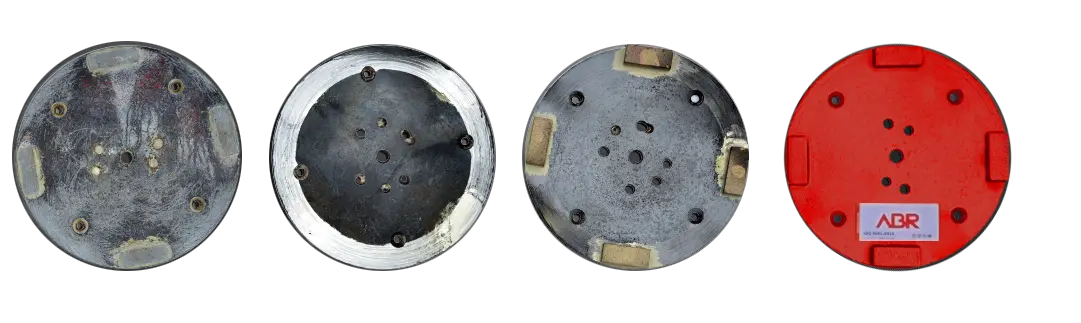
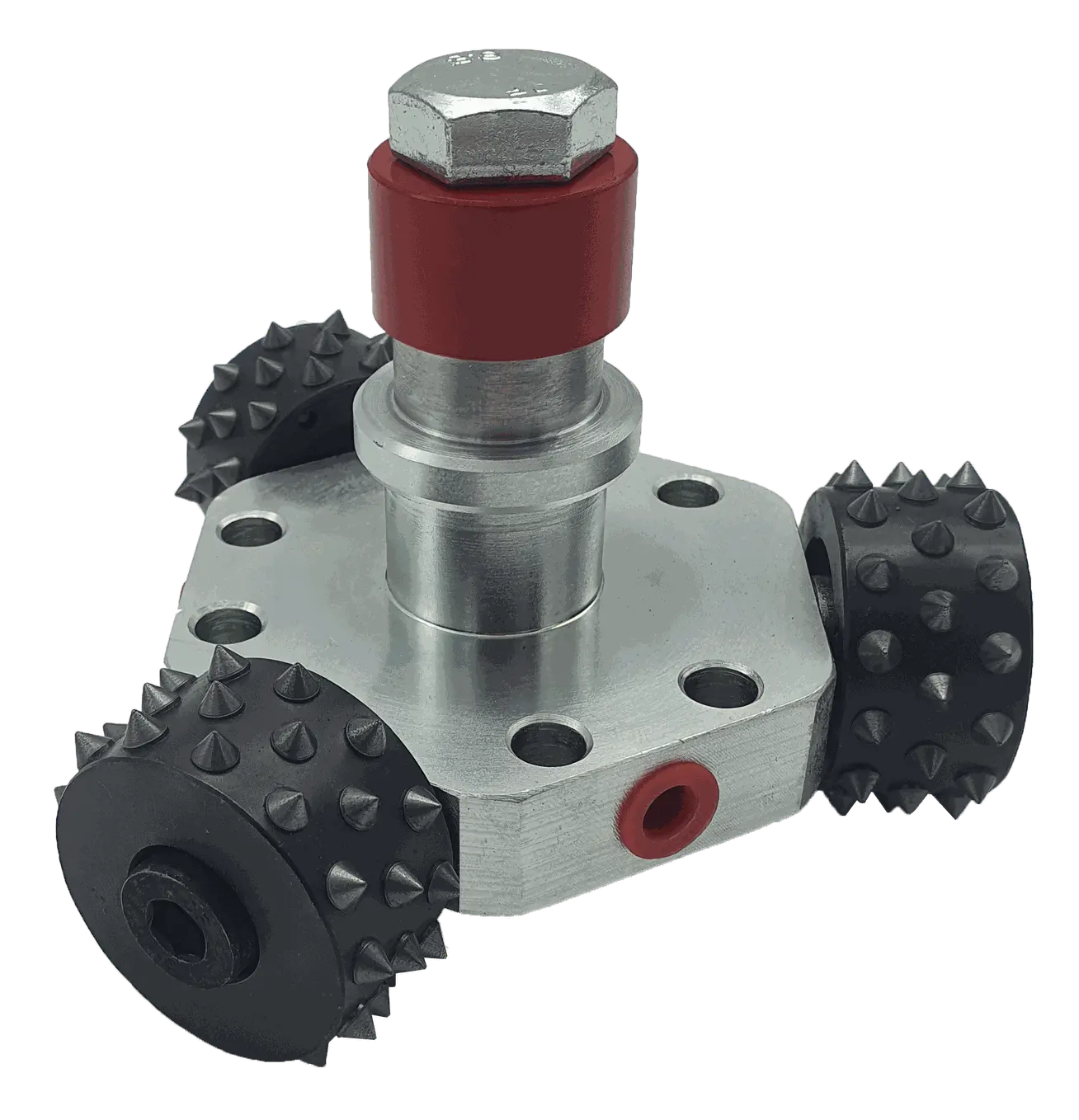
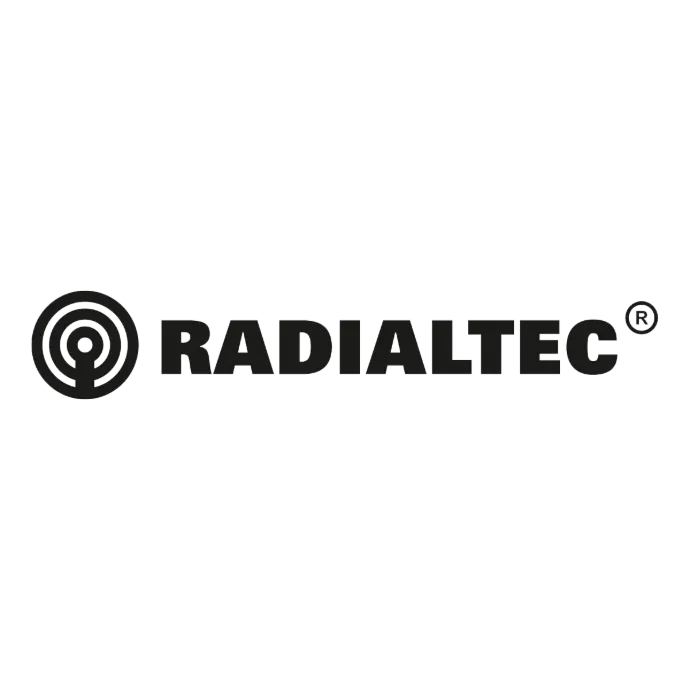

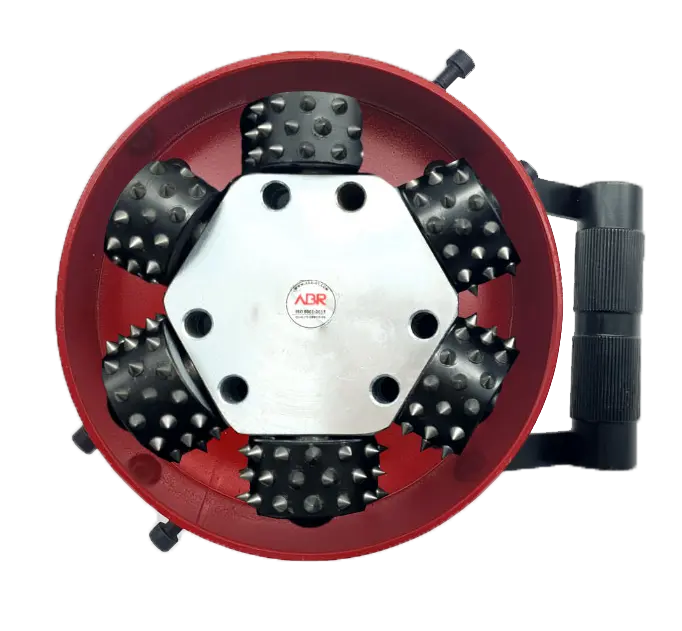
ABR’s patented radial technology provides an unprecedented increase in productivity, as well as an improvement in worker ergonomics, reducing the weight of the tool and avoiding annoying vibrations.
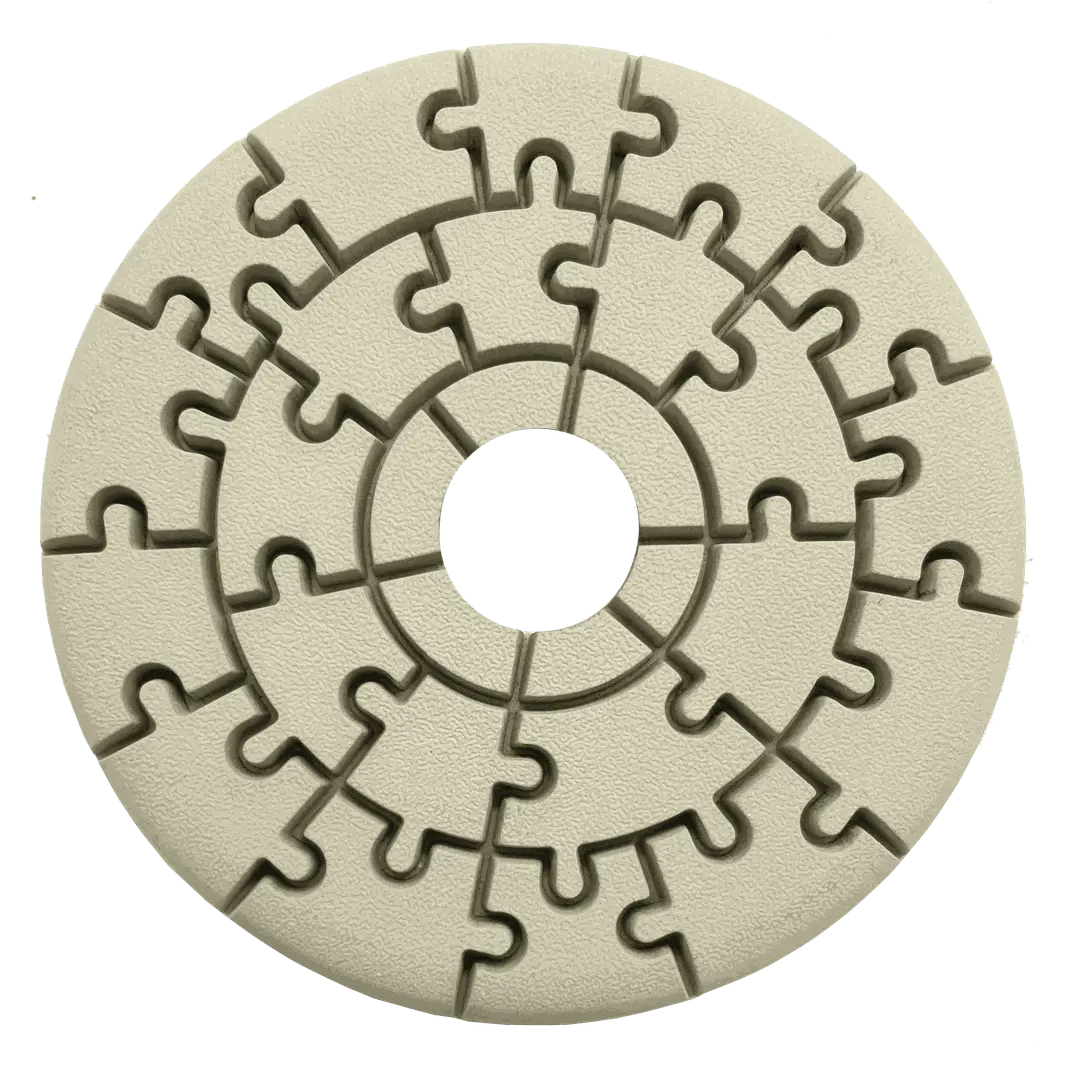
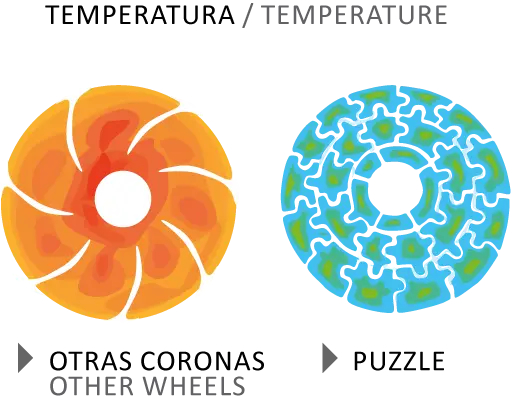
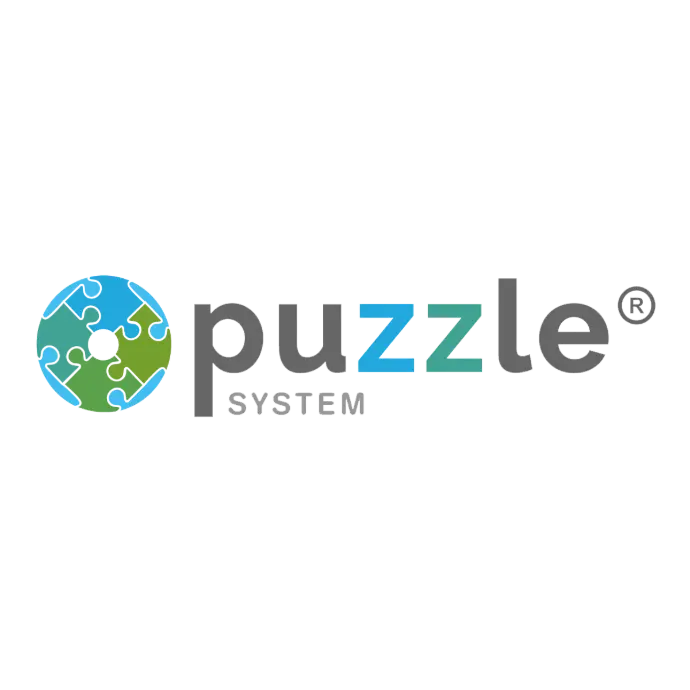
An innovative and highly efficient cooling system based on liquid cooling (watercooling). It keeps the tool cool and in optimal working condition throughout its entire lifespan.
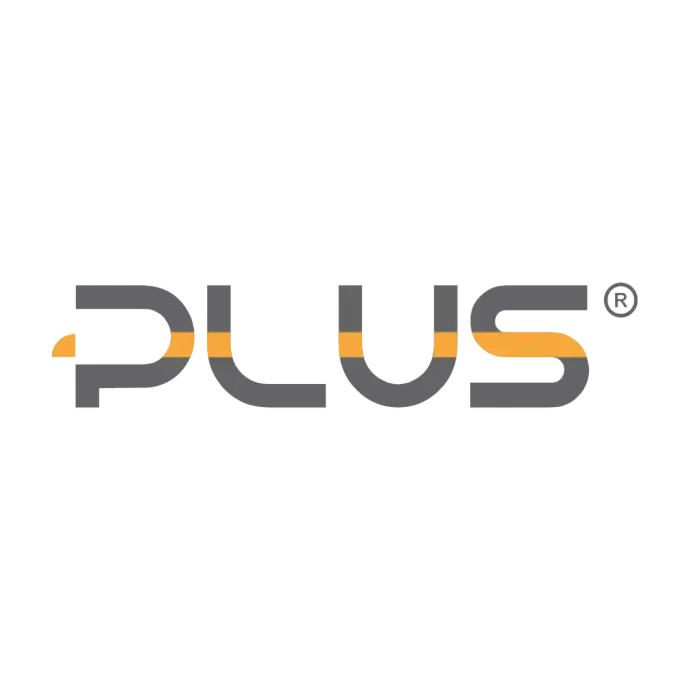
Internal structure with "double shielding," designed to withstand maximum loads, ensuring perfect operation under any conditions and throughout the rollers' lifespan. Maintenance-free due to its highly robust, self-lubricating internal construction and structural geometry.
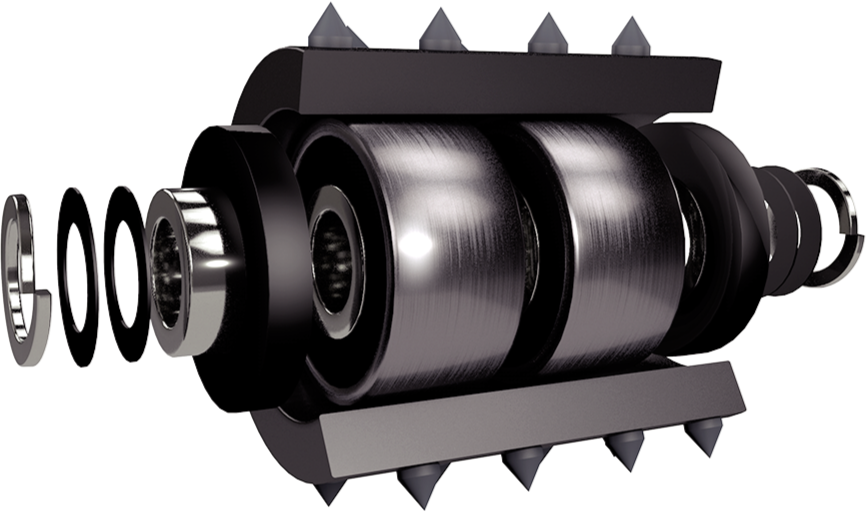
Maintenance-free armored structure ensures perfect operation under any conditions and throughout the life of the rollers.
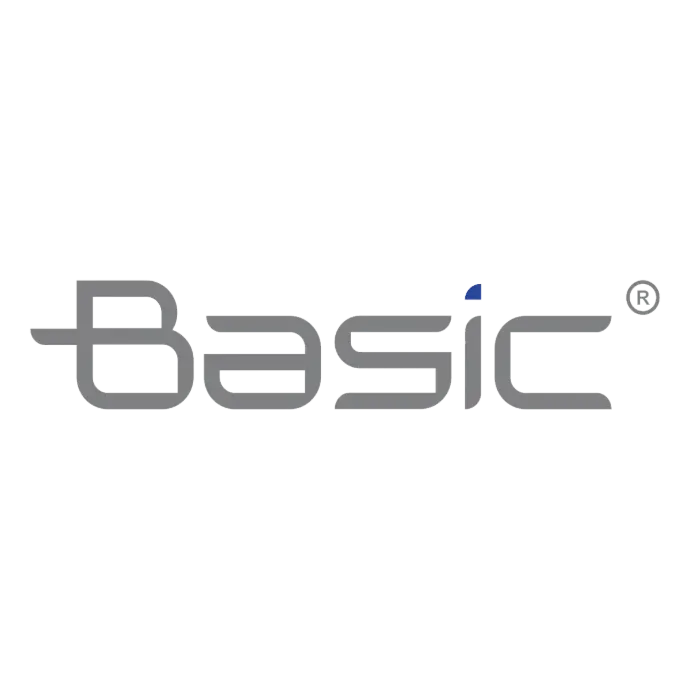
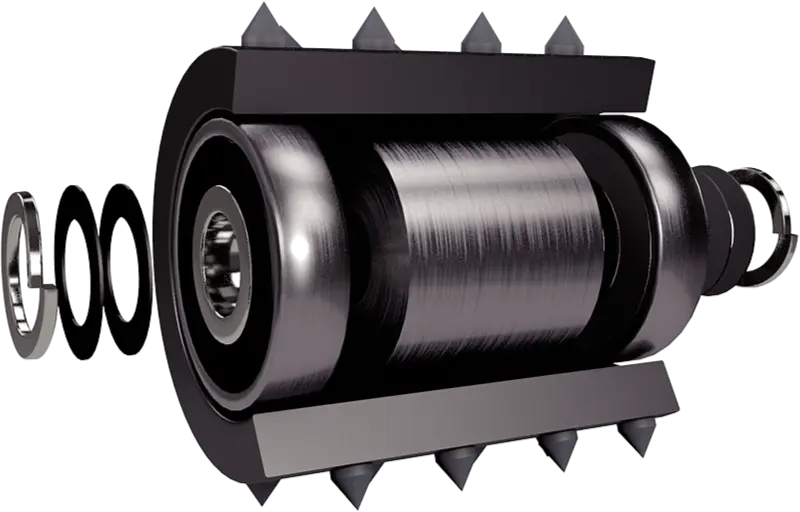
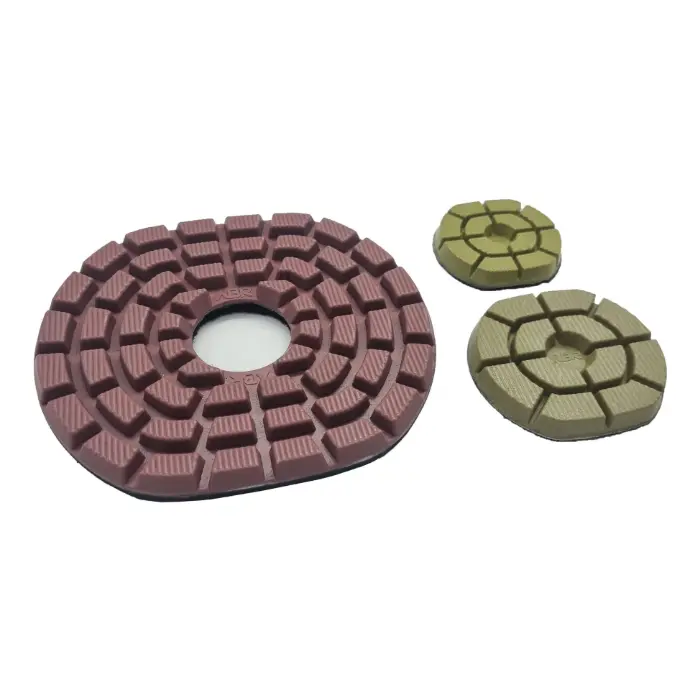
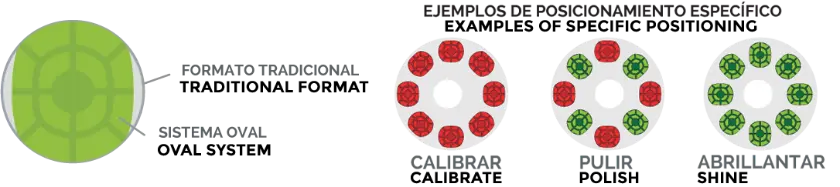
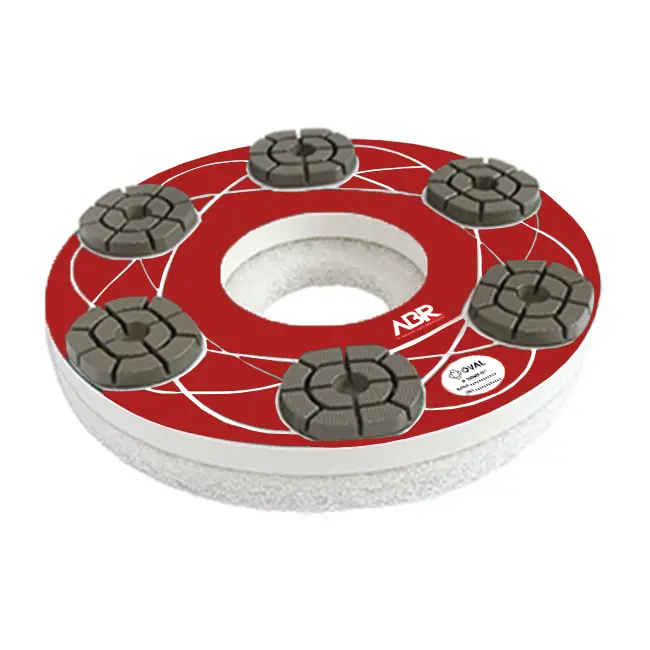
Thanks to the Oval design applied to ADR segments, we obtain tools with a standard diameter adaptable to all existing machines. We exponentially increase the work capacity, reducing the time and consequently the cost of polishing.

Magnetic clamping system, which guarantees a perfect and fast coupling of the tool to the machine. Possibility of installing this clamping system on CNC machinery as well as on traditional machinery.
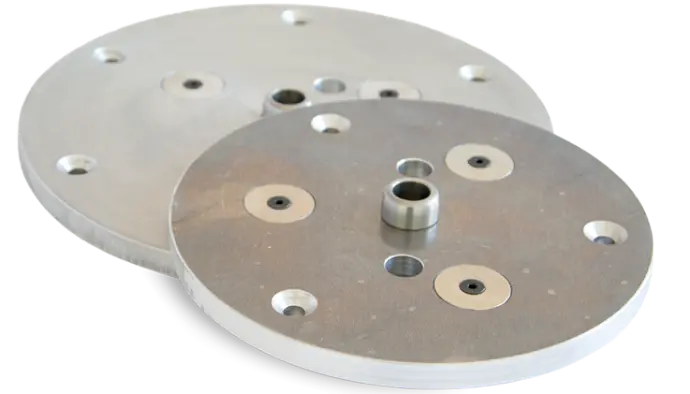
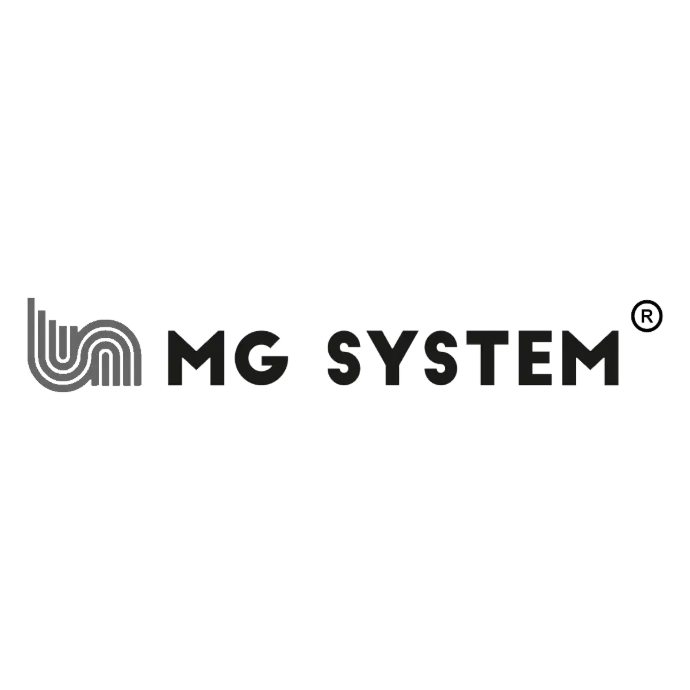
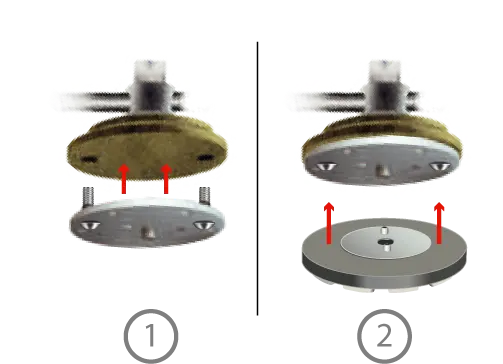
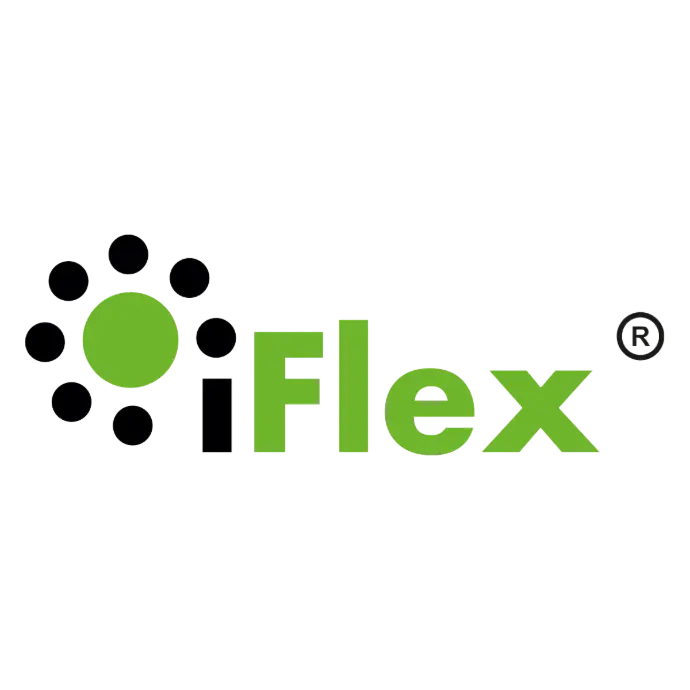
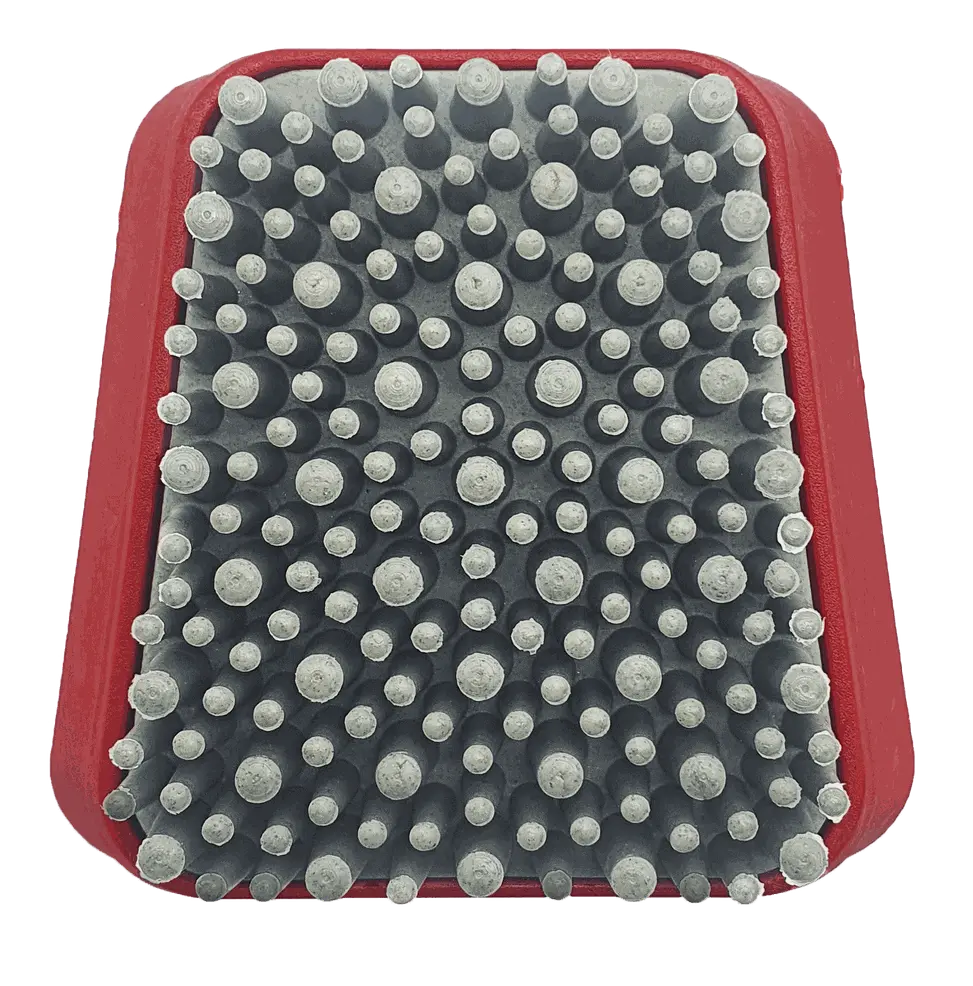
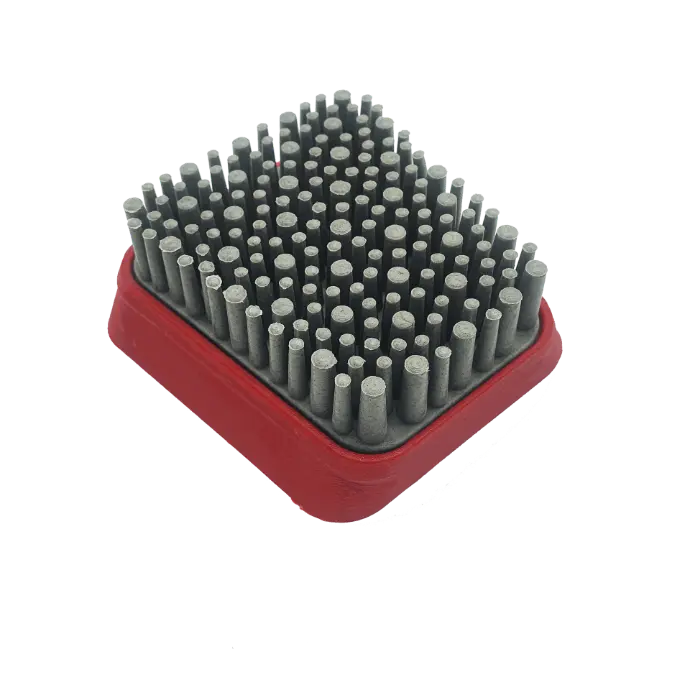
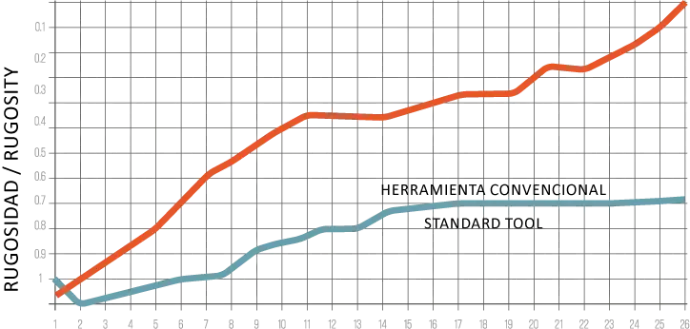
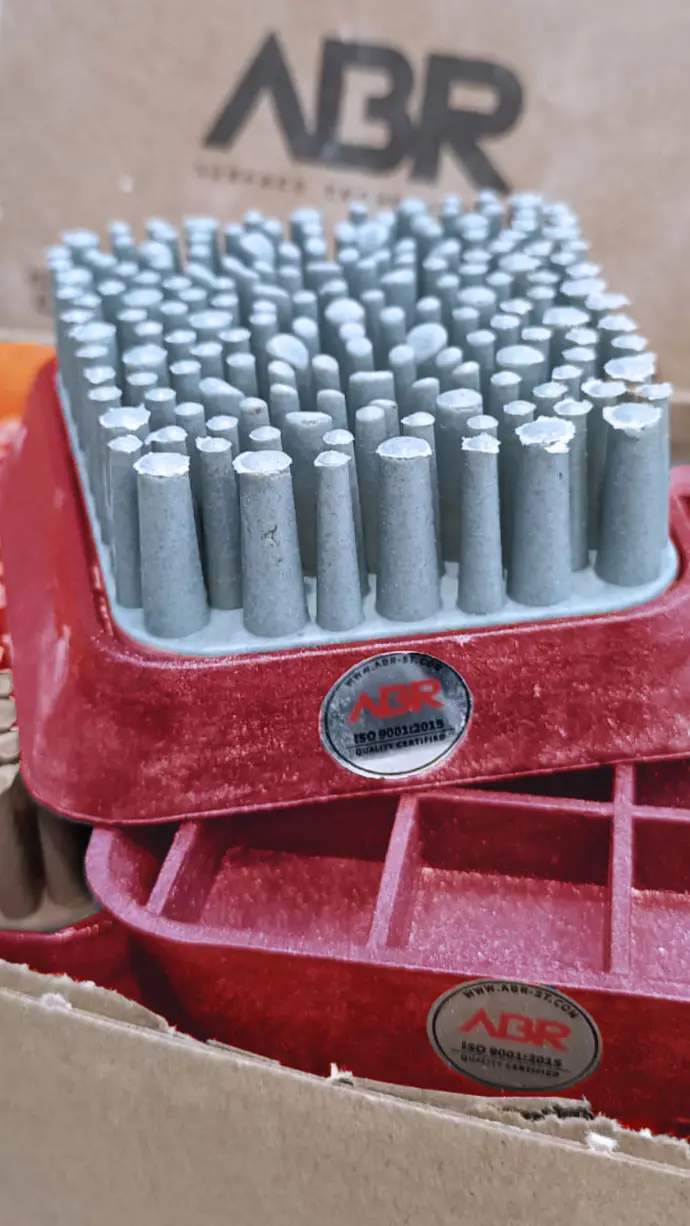
Based on the Fibonacci number series, semi-flexible products have been developed, achieving effective surface texturization.
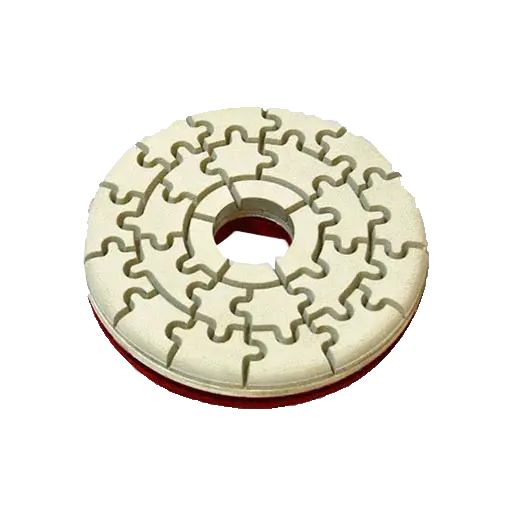
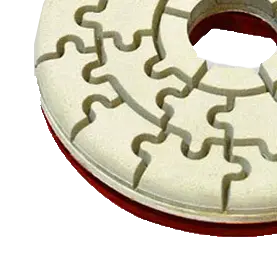
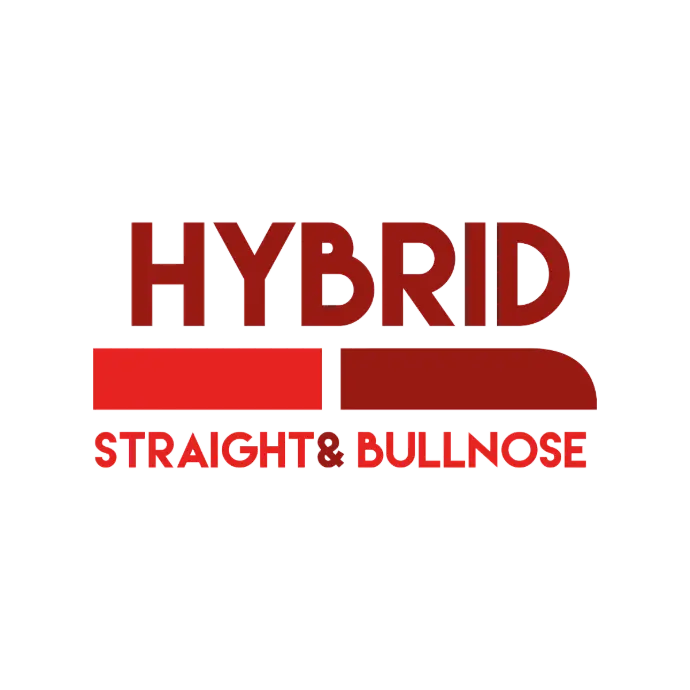
The unique crisscross designs of this technology allow for the manufacture of cutting-edge tools for use on both straight and curved surfaces.
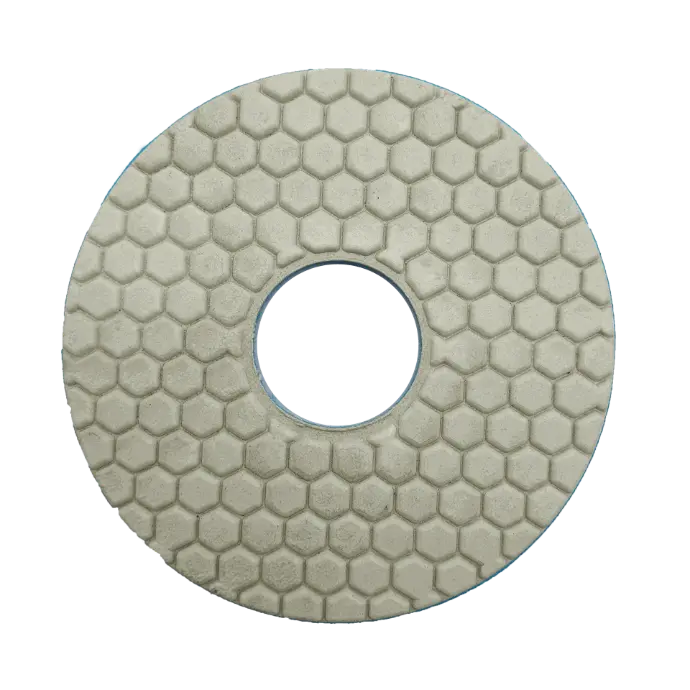
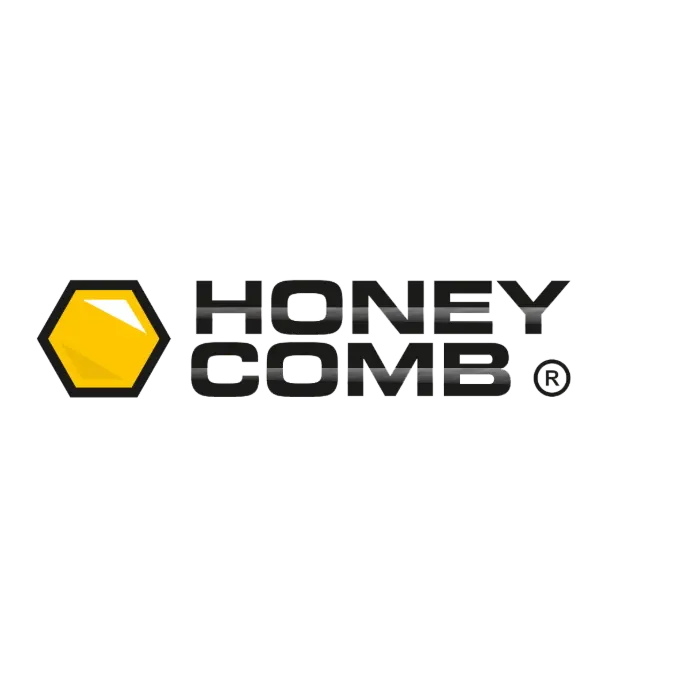
The geometrical honeycomb structure is the ideal basis for building products with a very strong yet lightweight structure, providing perfect cooling during use.
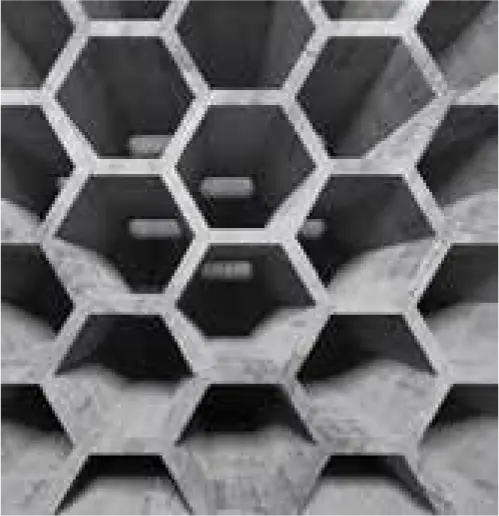
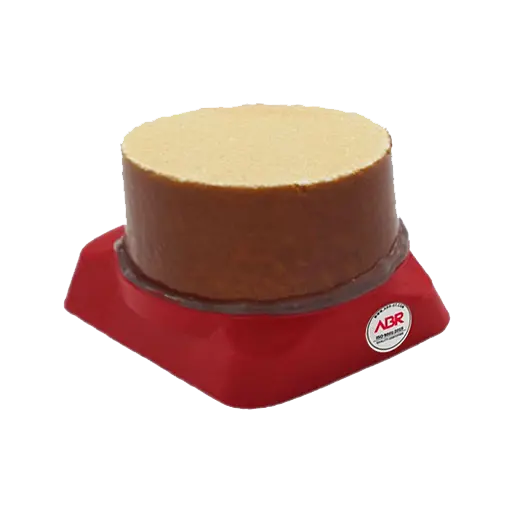
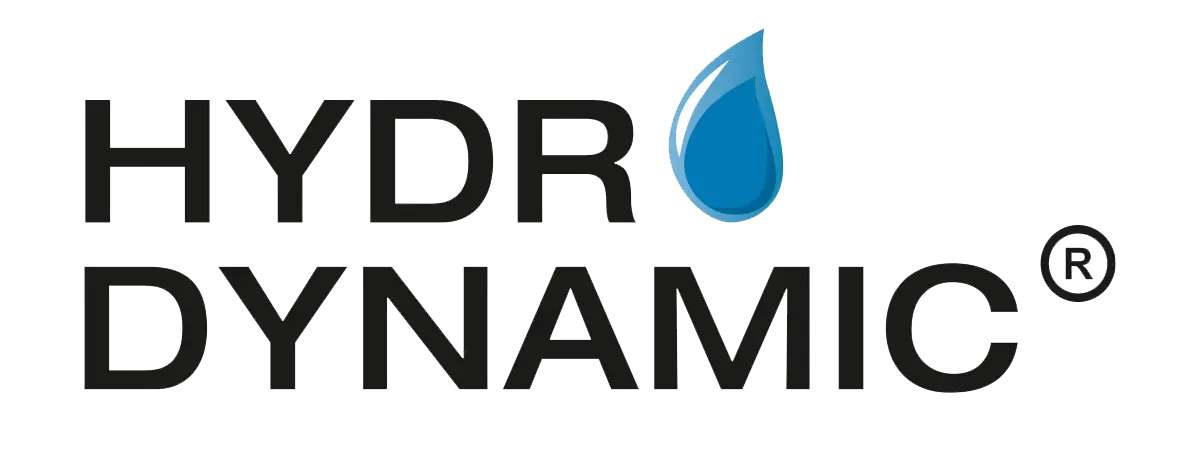
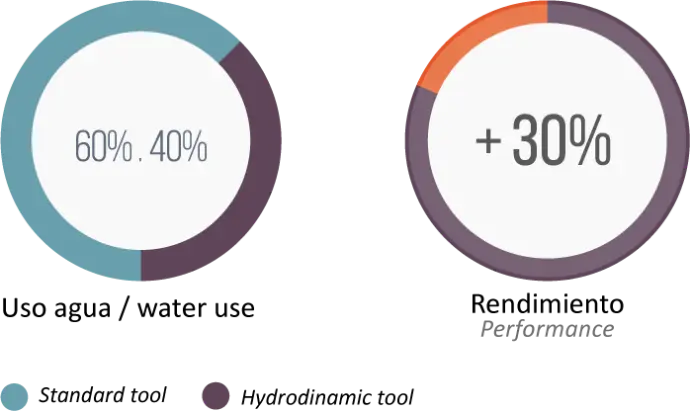
The PATENTED hydrodynamic shape reduces water consumption and achieves higher performance.
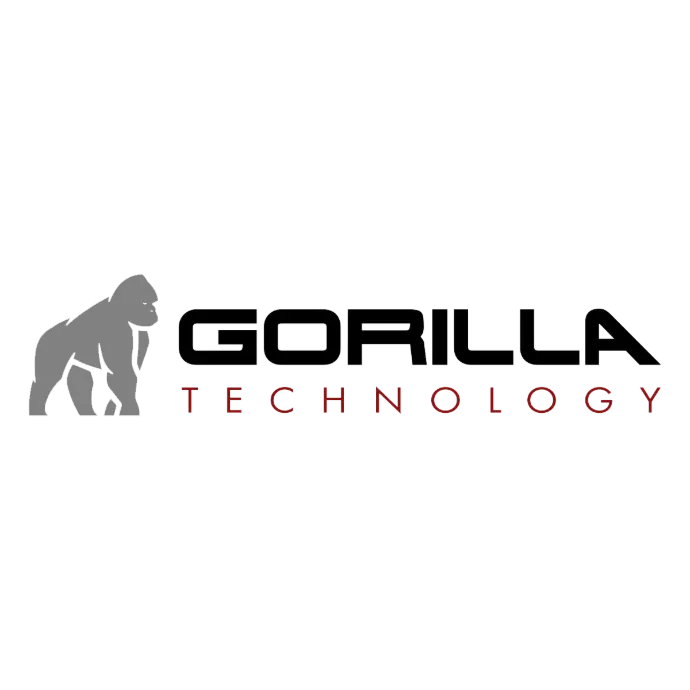
With this technology, combined with a careful selection of raw materials and an elaborate production process, we create an extra-hard glass on the polished surface of marble or terrazzo. It increases the surface's hardness on the Mohs scale and increases its scratch resistance.
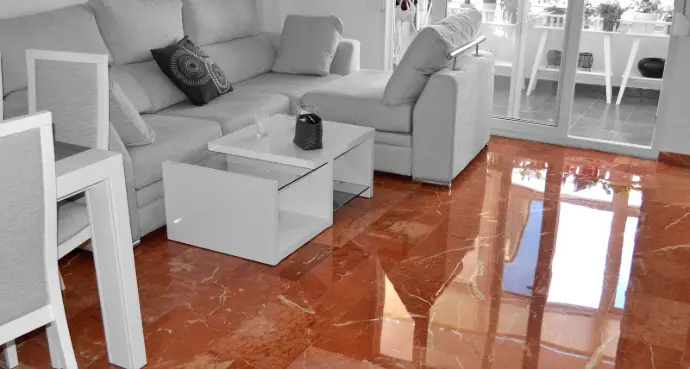
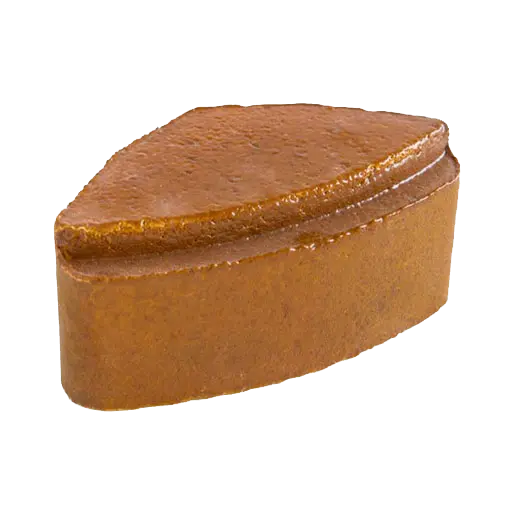
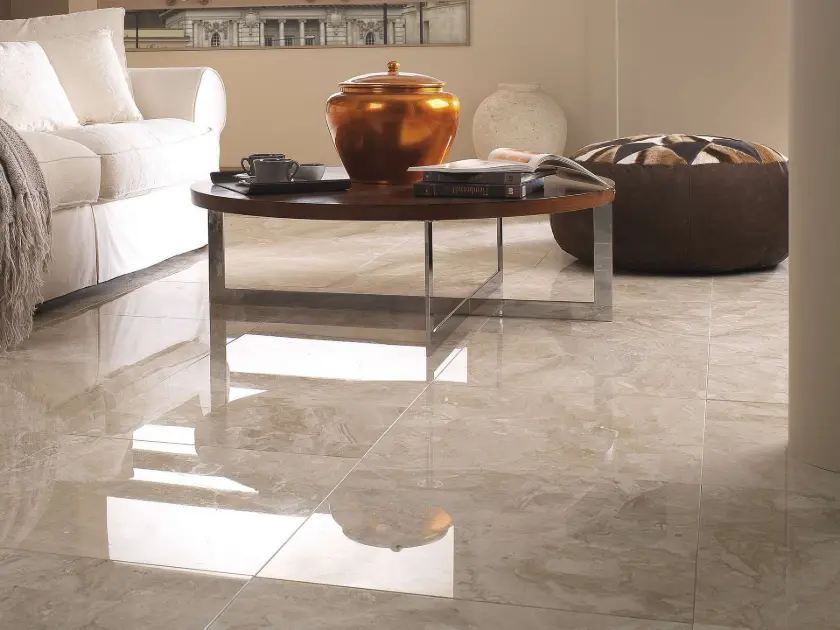
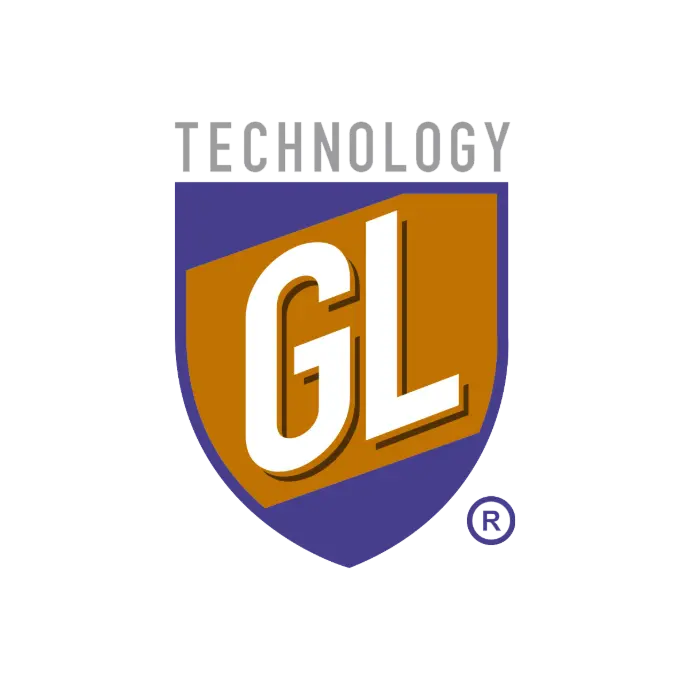
GL hardnesses are designed to polish the most demanding marbles, where we are looking for a mirror shine with maximum depth without sacrificing performance. This GL technology combines natural raw materials of animal origin with an extremely careful and handcrafted manufacturing process, ensuring the highest product quality
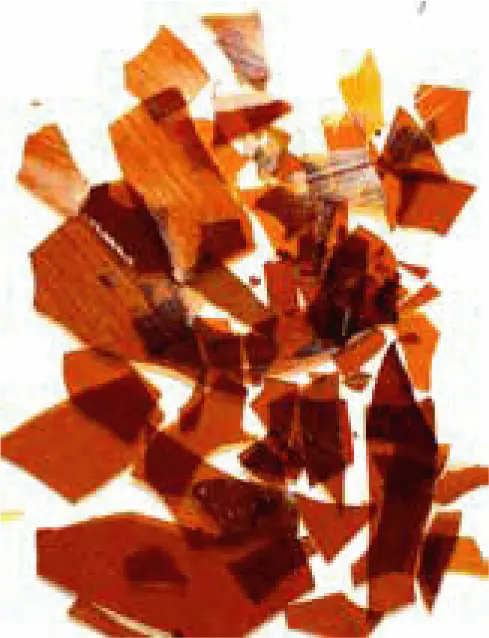
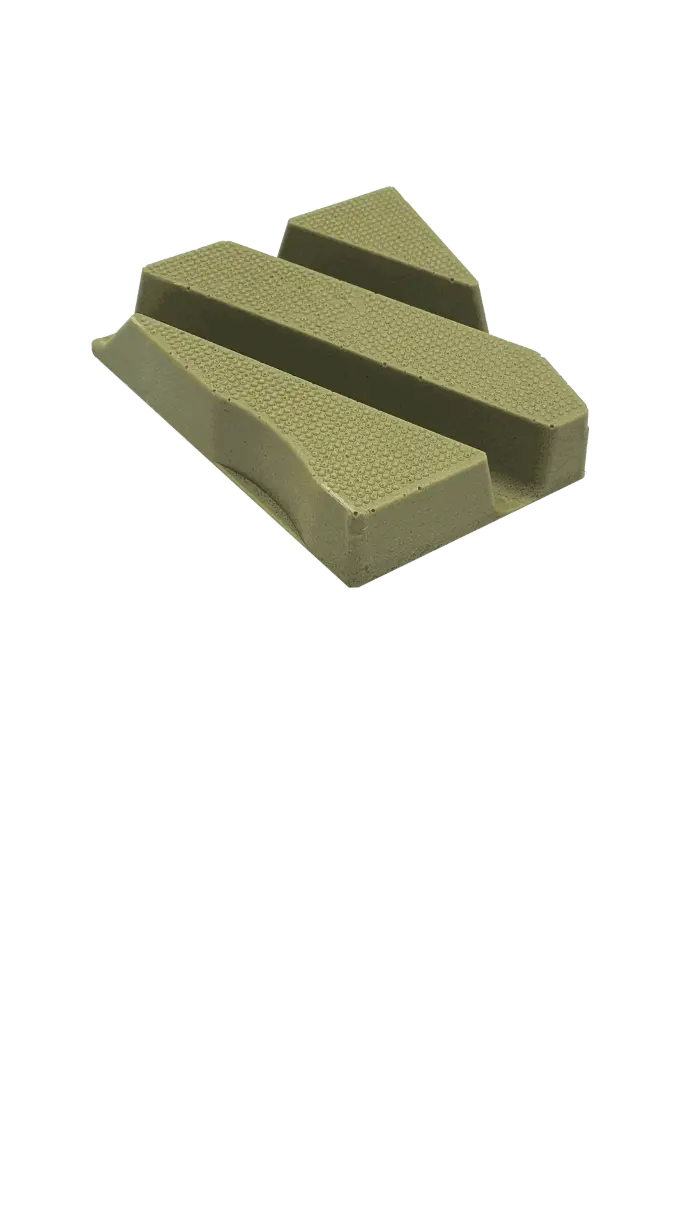
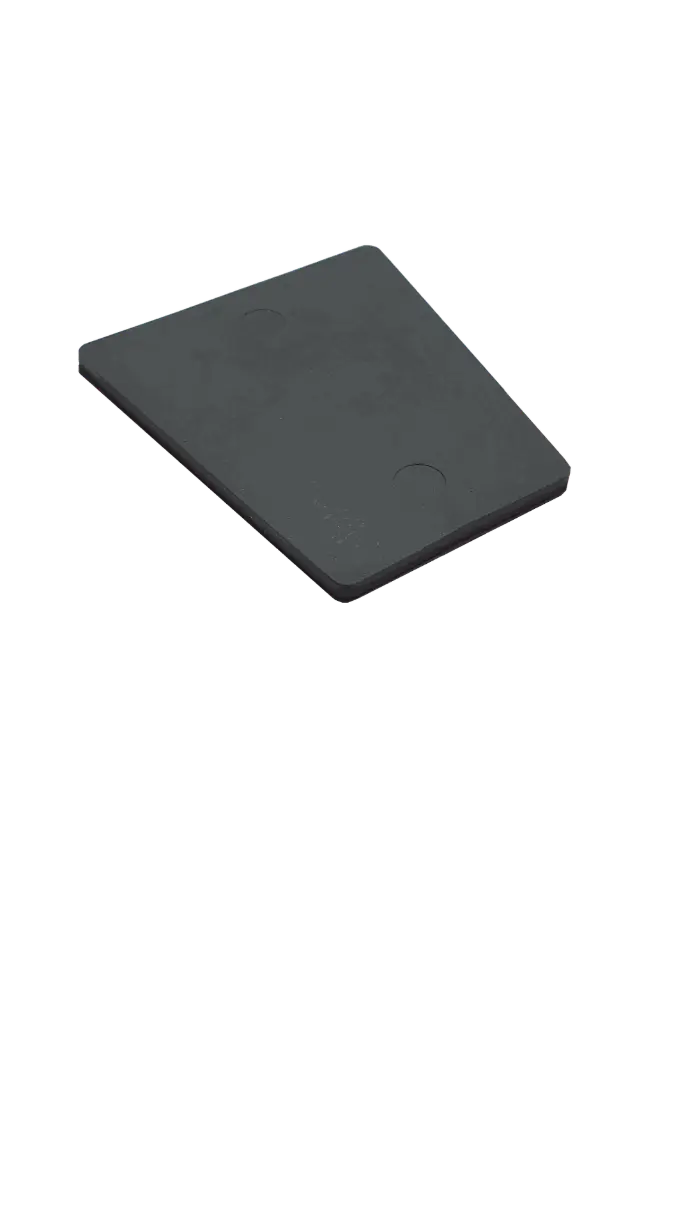
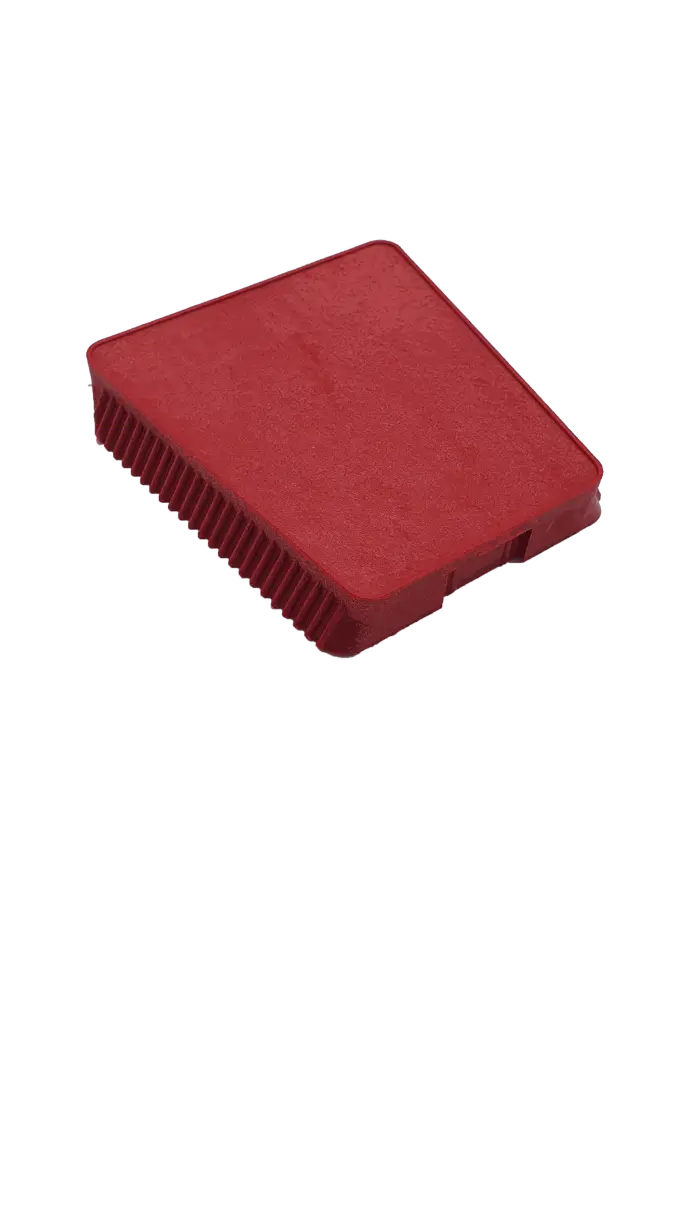
Flexible technology for exquisite care of the surfaces to be polished. The tool's construction, combining flexible and rigid parts, ensures perfect fit and constant contact with the surfaces, avoiding marks and scratches during polishing.
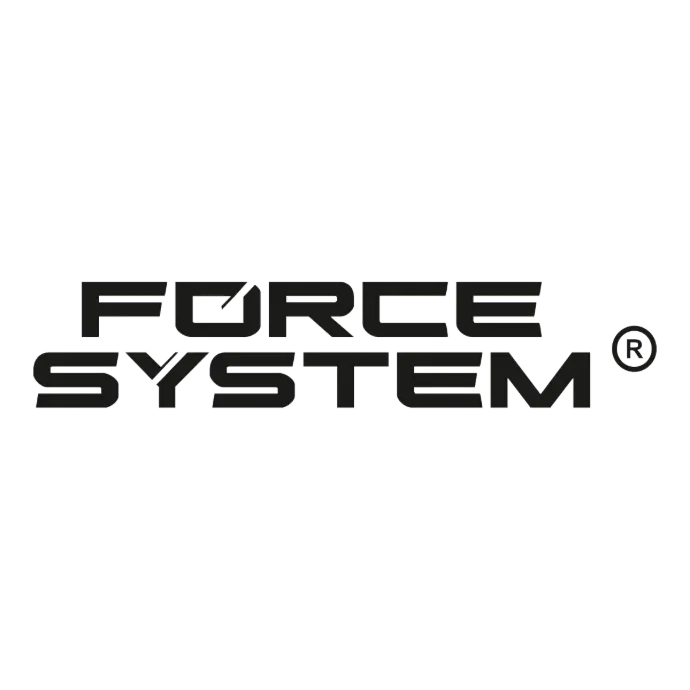
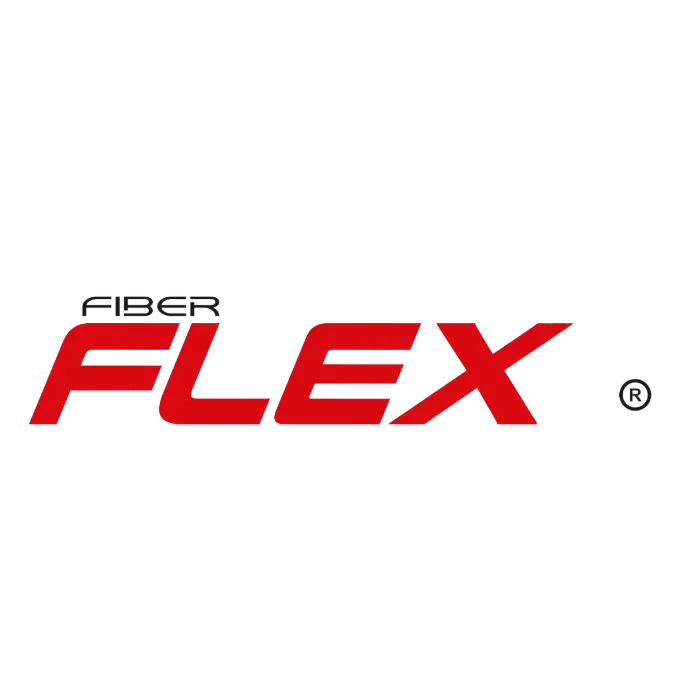
The combination of synthetic fibres with highly flexible resins makes it possible to create innovative diamond abrasives. Toughness and lightness are the main characteristics of this new technology.
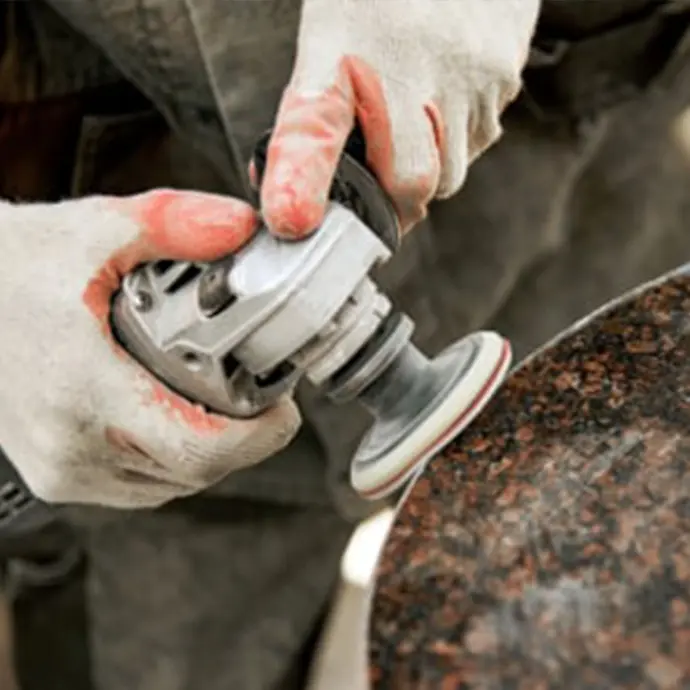
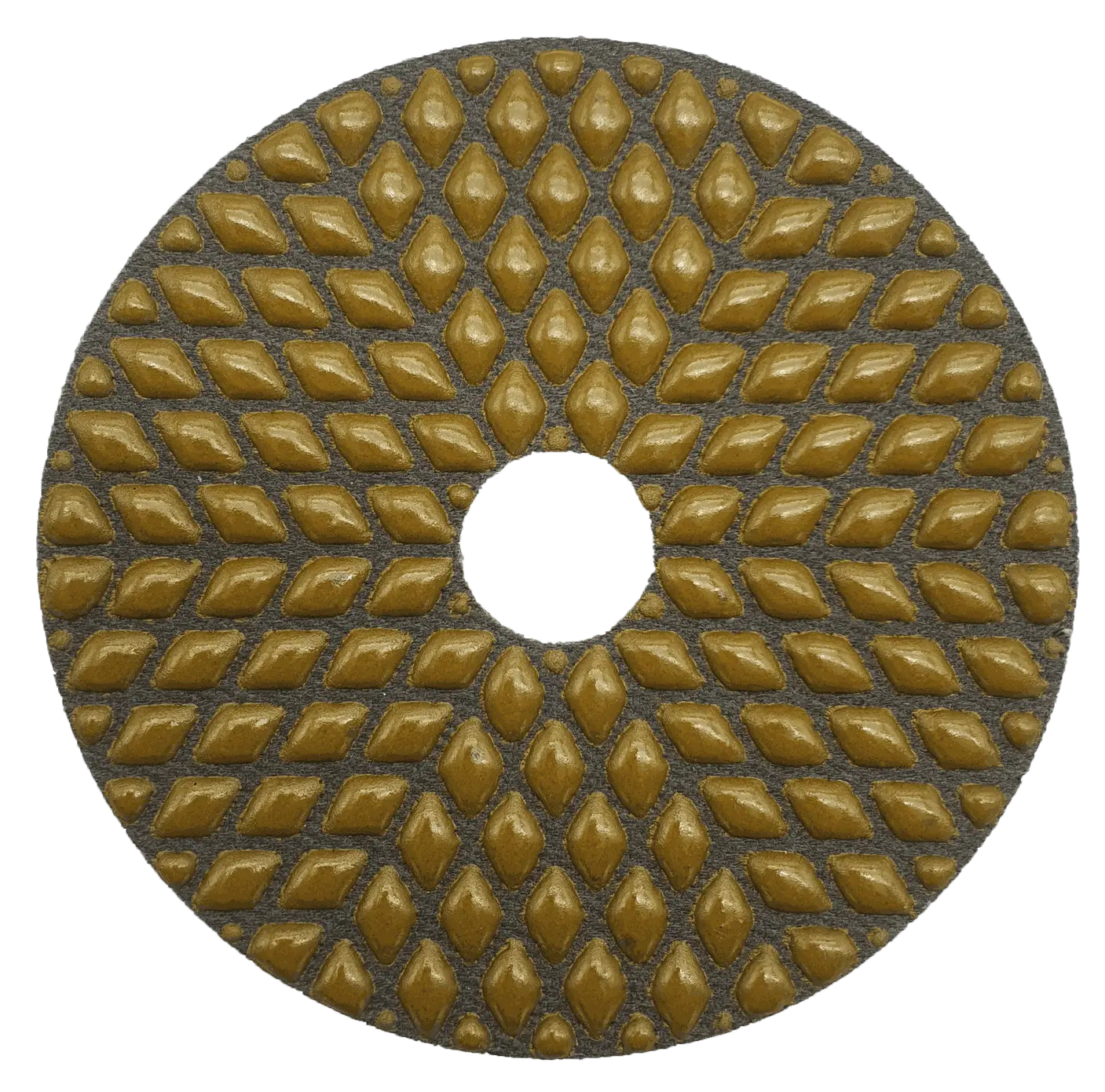
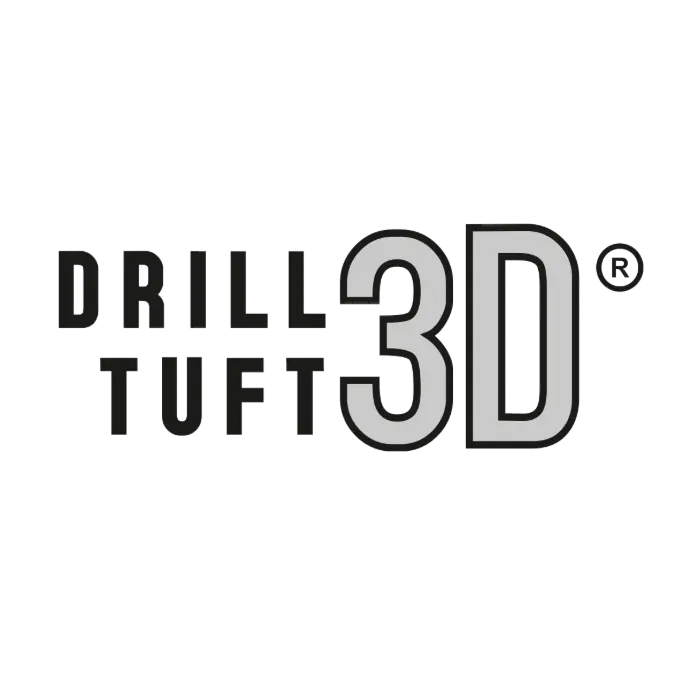
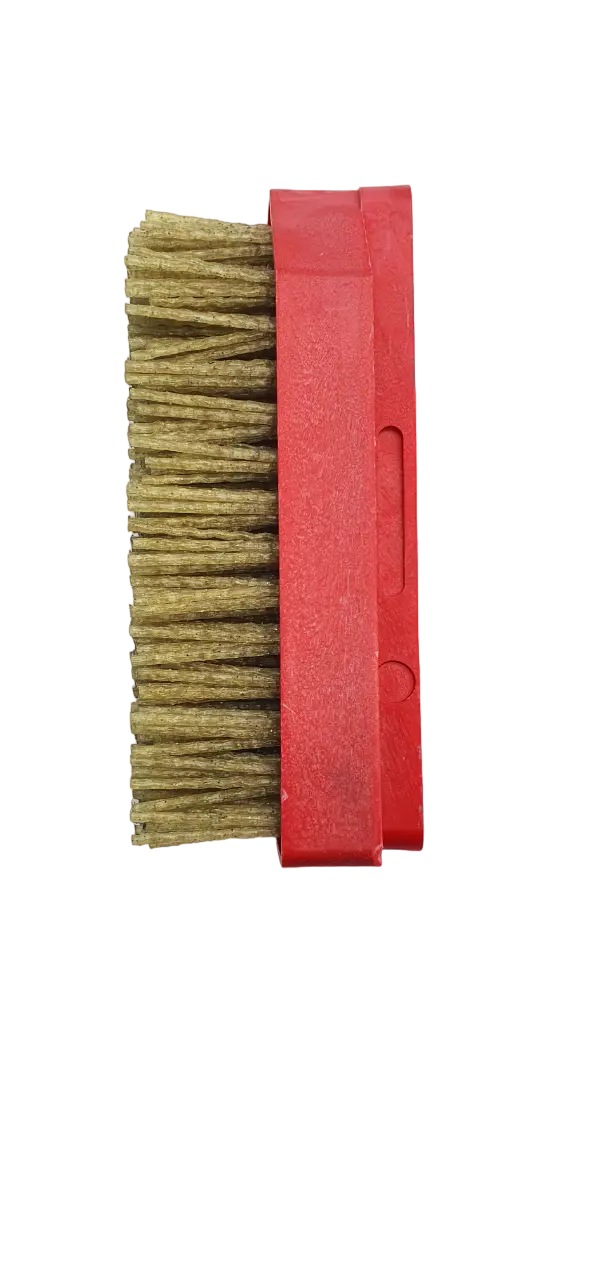
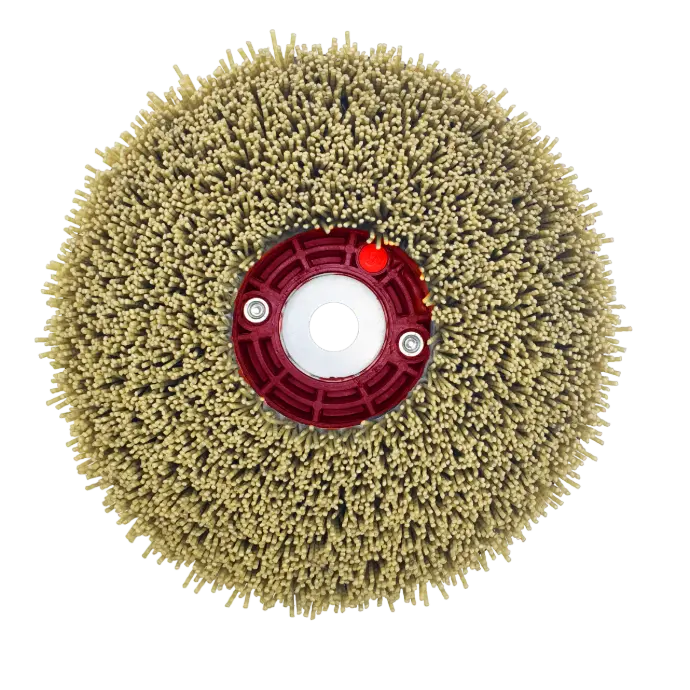
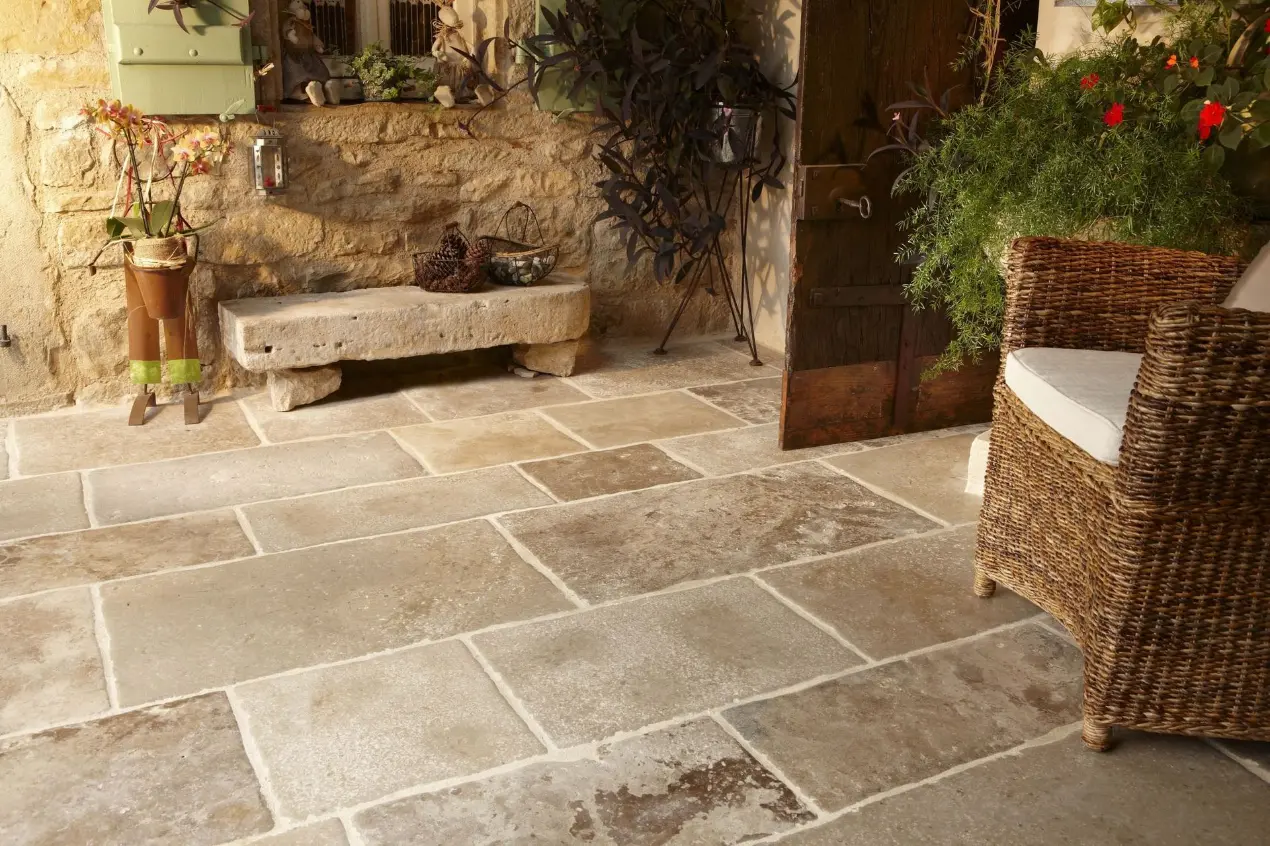
Technology that combines 3D CAD design with the construction of the support and the insertion of the filaments in a single production order, making it possible to manufacture technical brushes with maximum precision and efficiency.

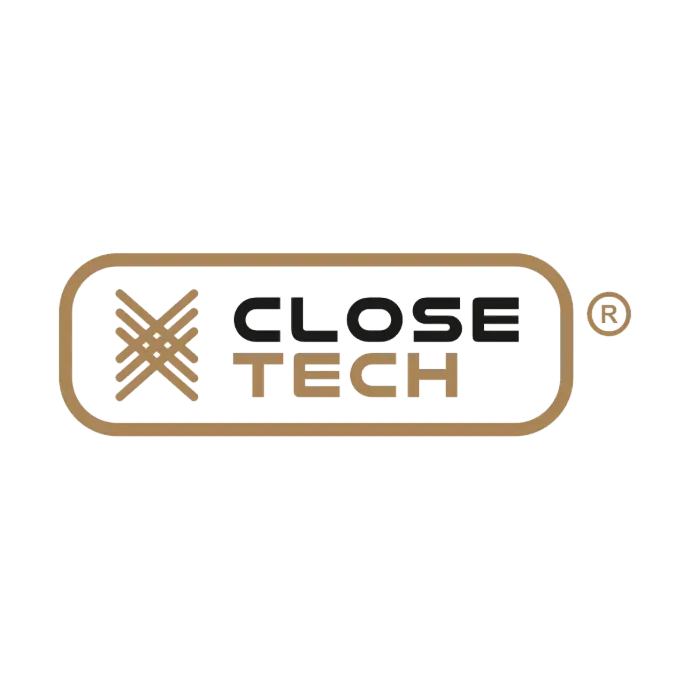
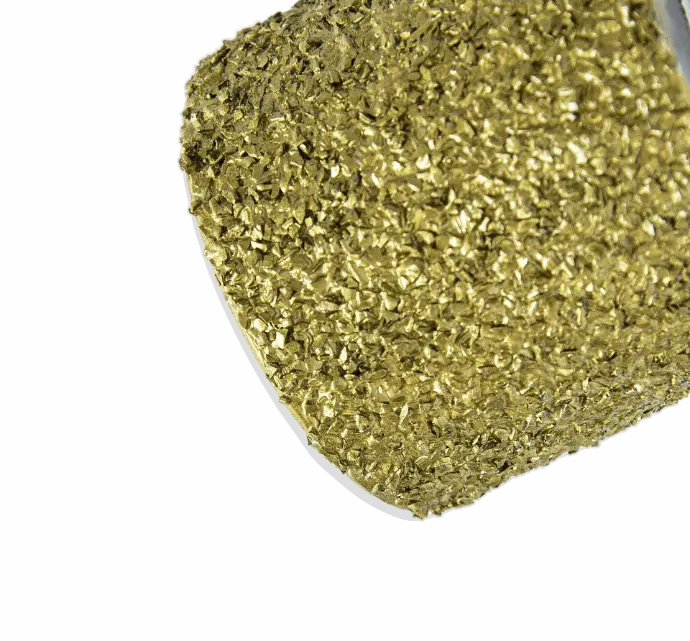
Closed mechanical electrostatic dispersion improves the positioning of Widia grains, complying with FEPA regulations and achieving tools with very low wear and maximum precision.
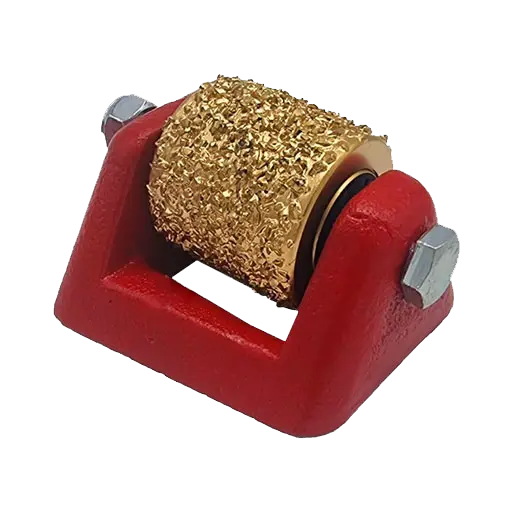
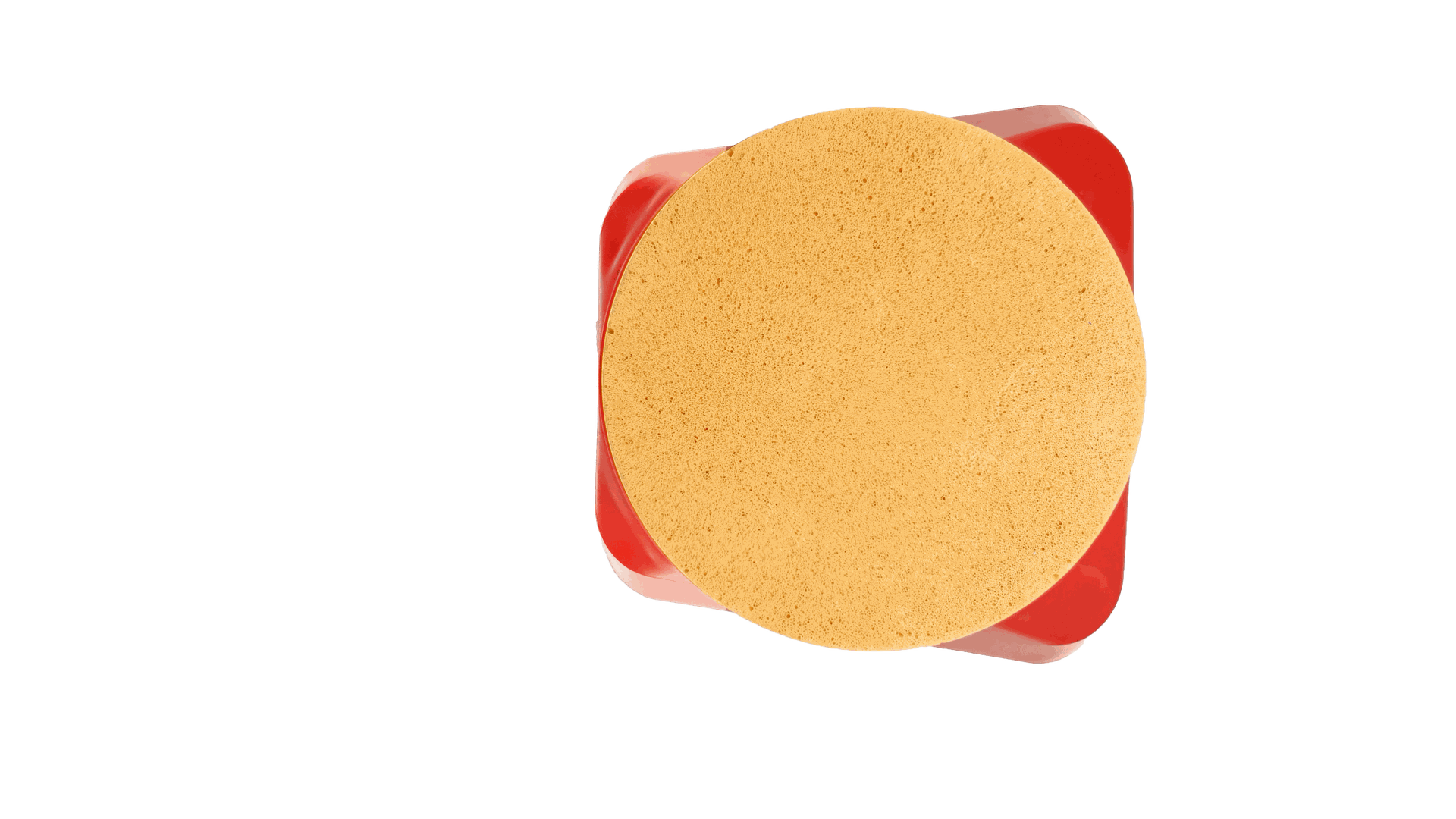
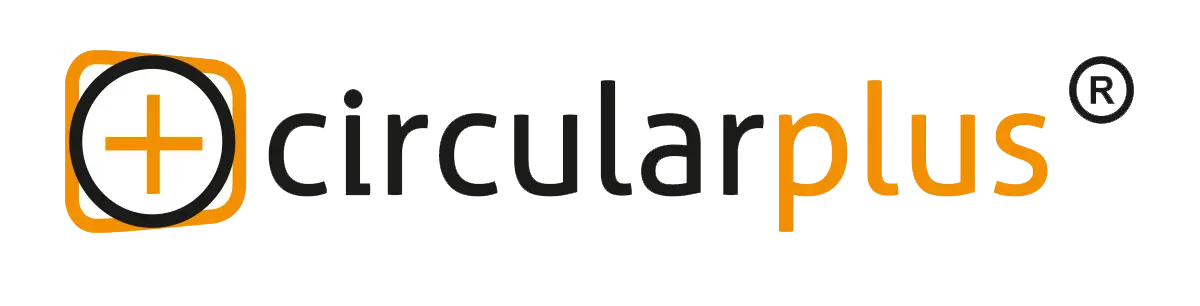
By means of the PATENTED circular shape we are able to build tools with maximum density on traditional non-circular supports. The result is high performance tools with maximum efficiency.
A controlled and homogeneous dispersion of the diamond makes this technology the perfect combination to obtain specific diamond abrasives for ceramics.
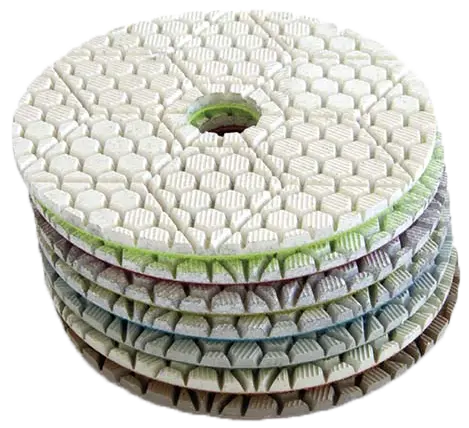
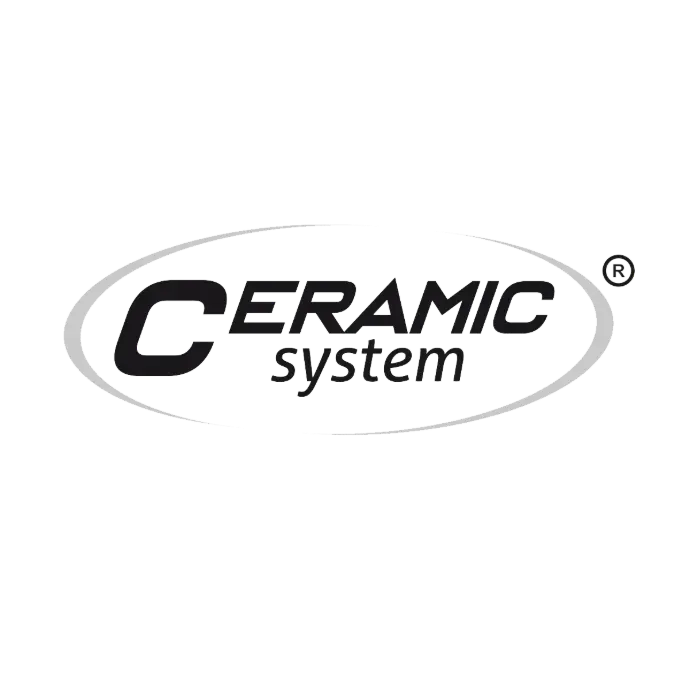
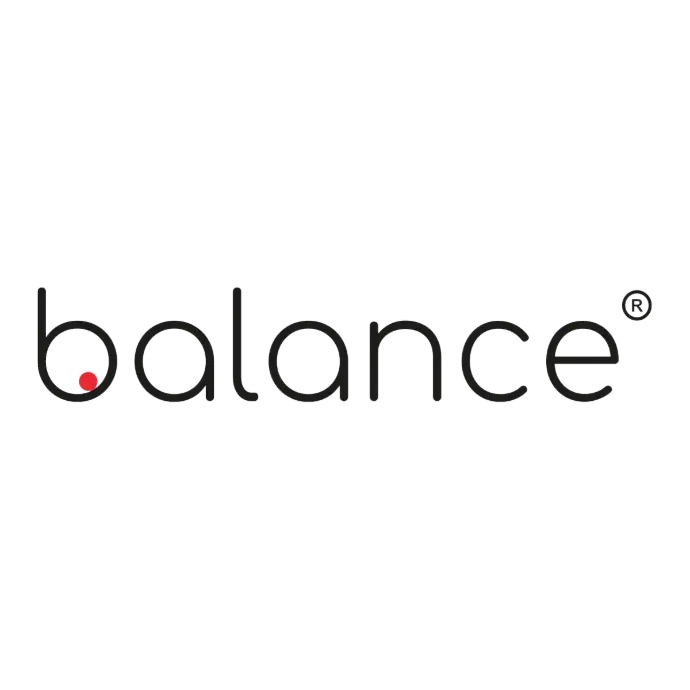
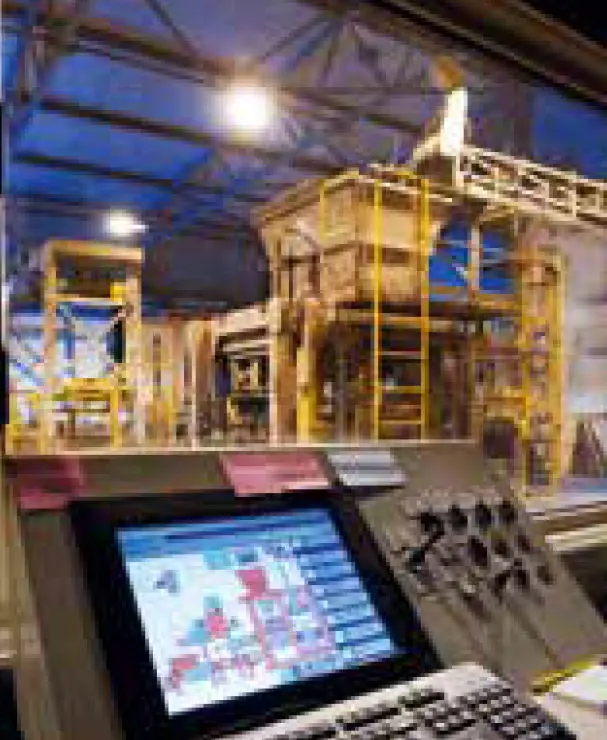
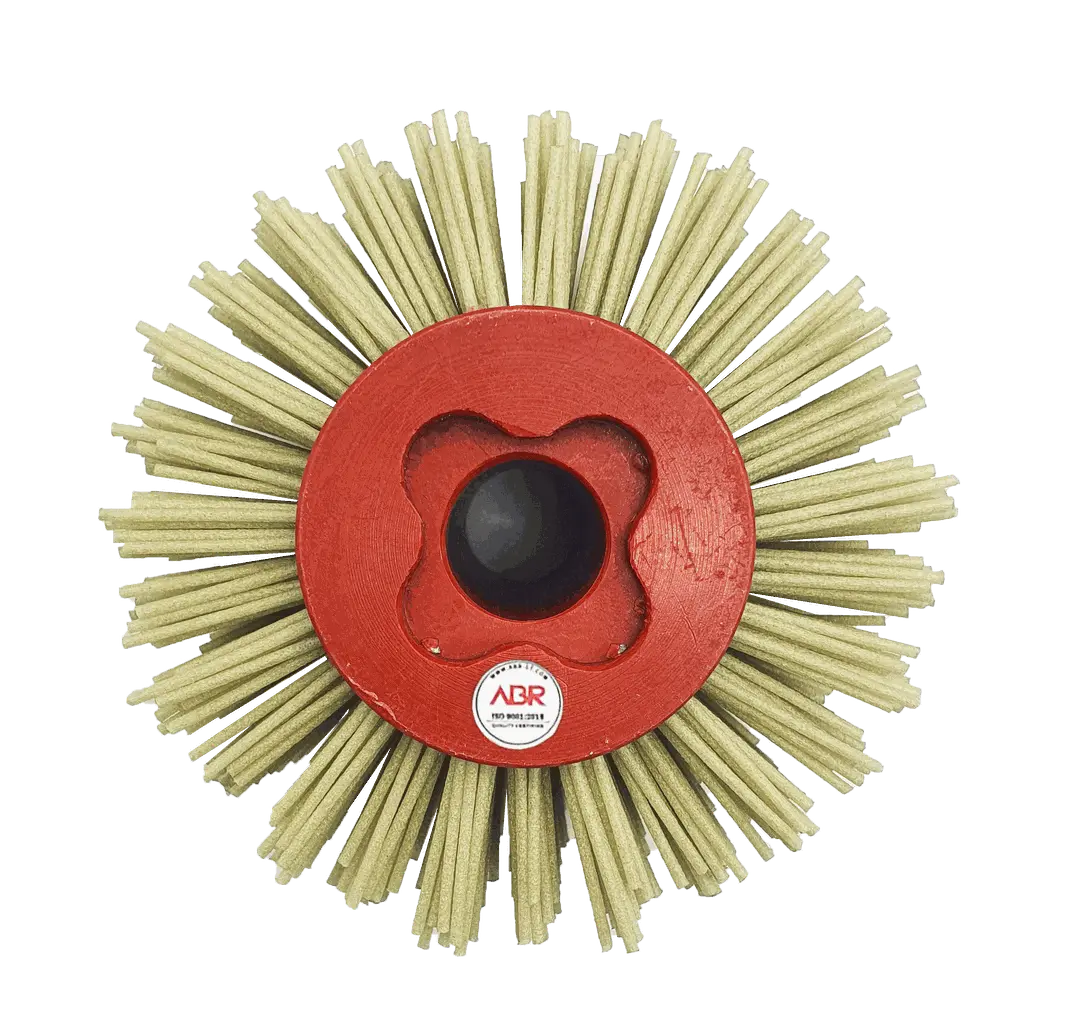
Balancing system for portable tools. It eliminates vibrations and protects the machinery against possible breakdowns. It also substantially increases the useful life and precision of the tools.
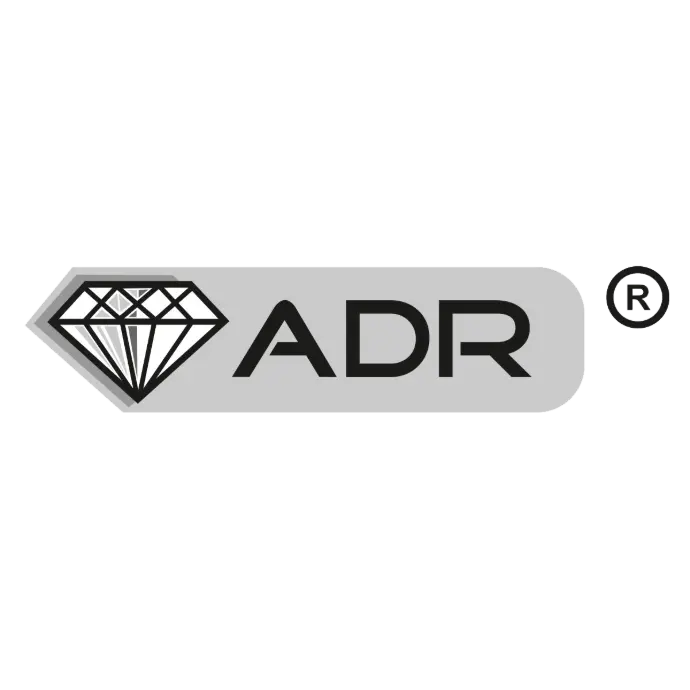
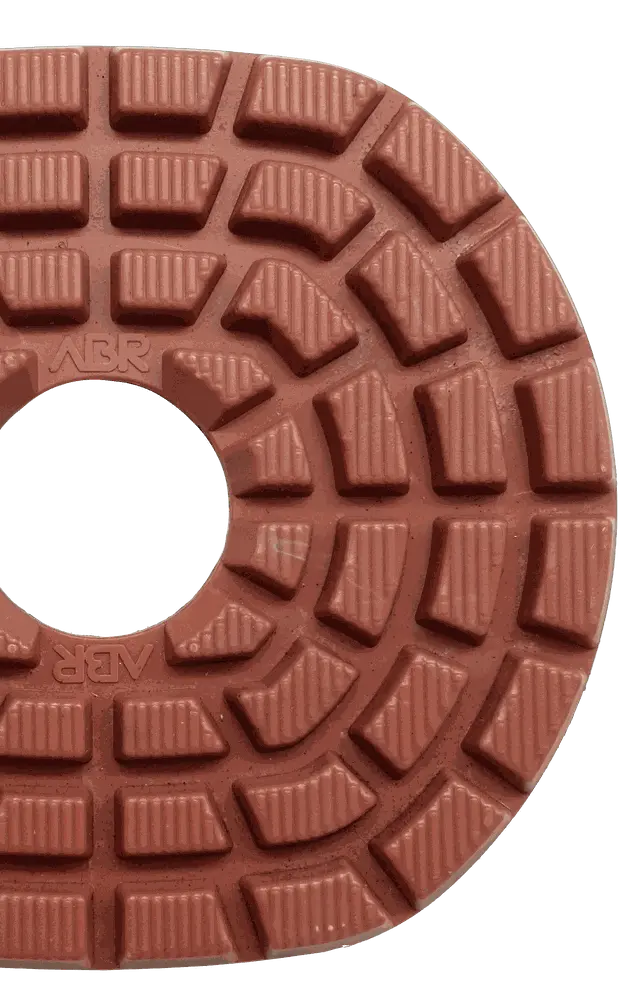
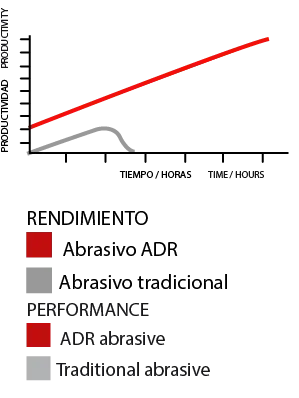
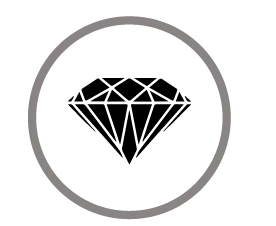
A controlled and homogeneous dispersion of diamond makes this technology the perfect combination for achieving superior diamond abrasives.
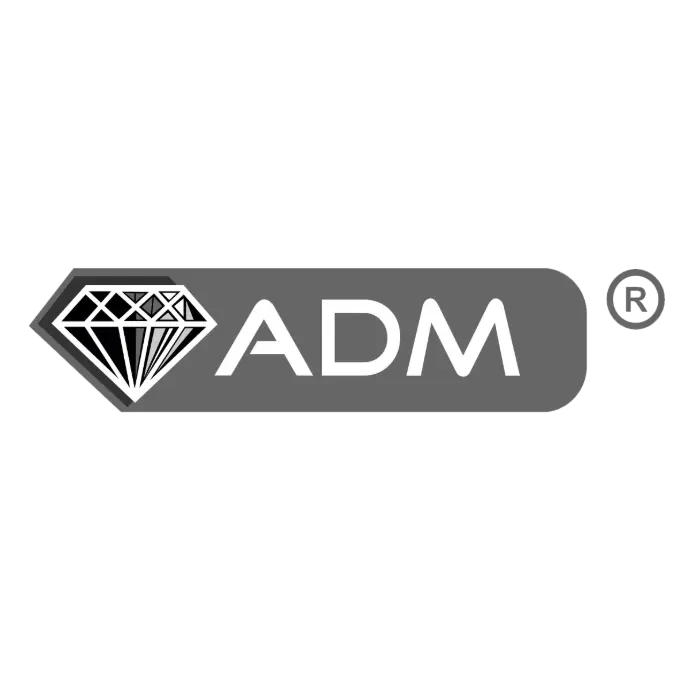
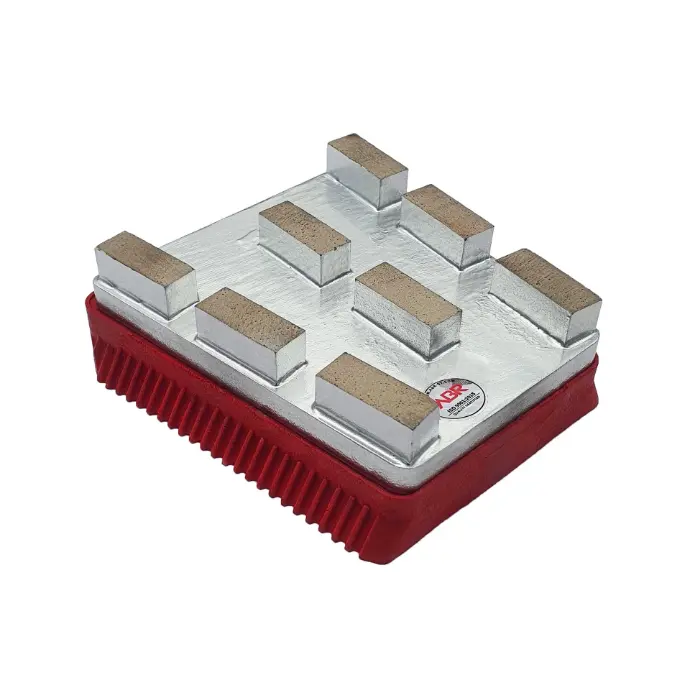
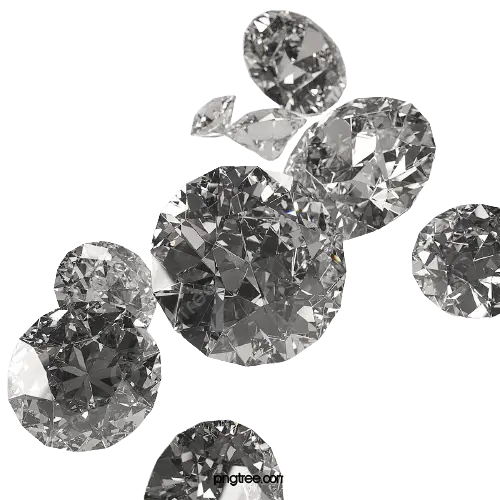
A controlled and homogeneous diamond dispersion makes this technology the perfect combination for superior diamond abrasives.
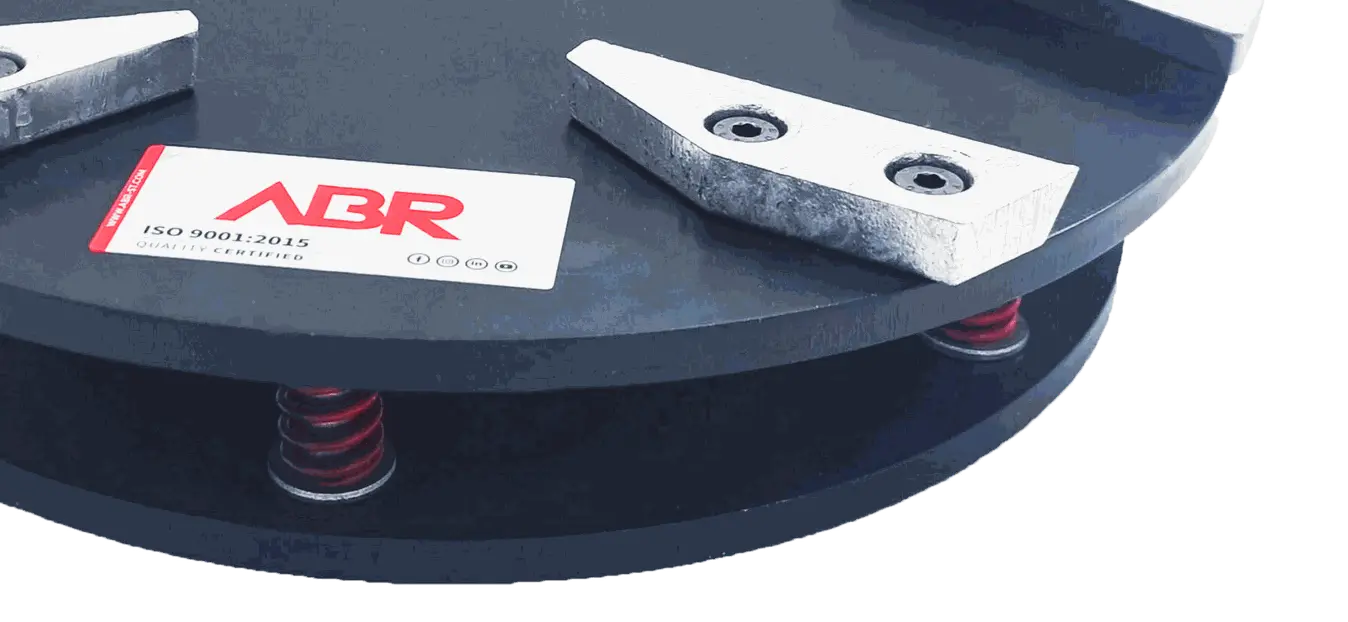
Revolutionary Axial Kit consisting of an axle and four shock absorbers with variable spring-type geometry. Thanks to this system it is possible to effectively absorb the shocks received by the rollers during their work.
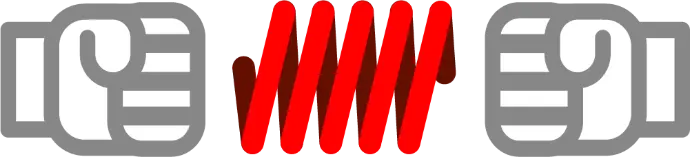
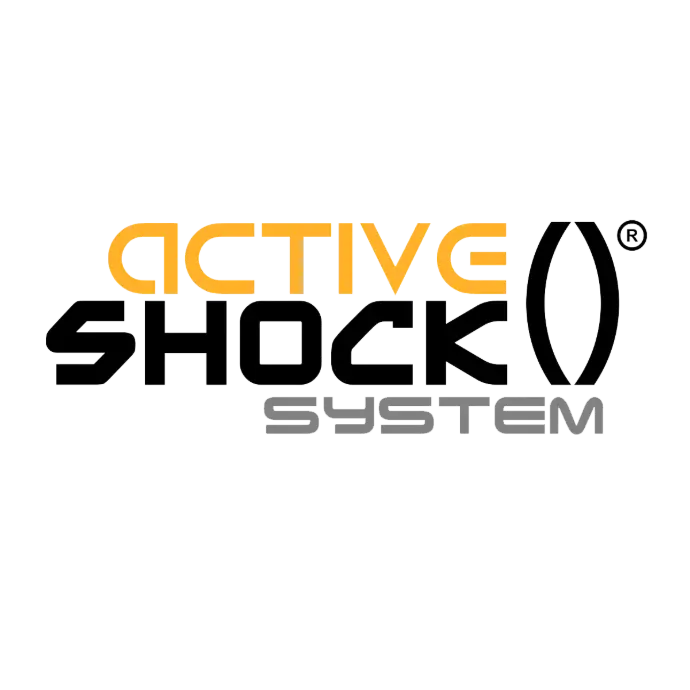
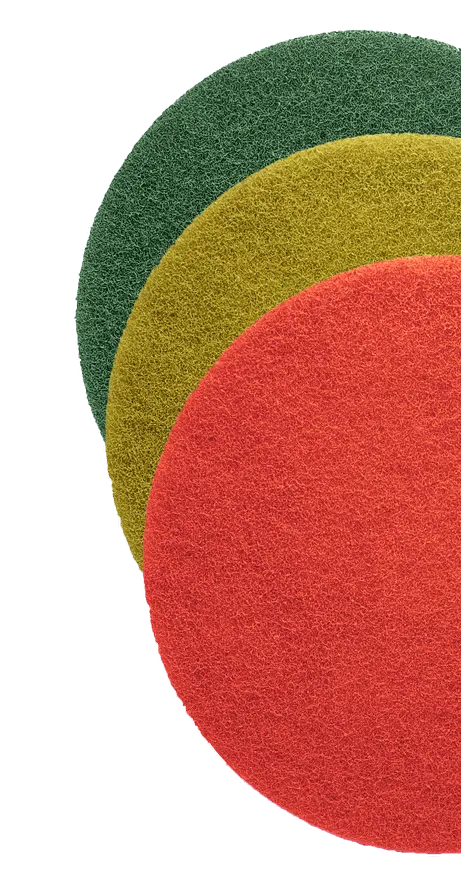
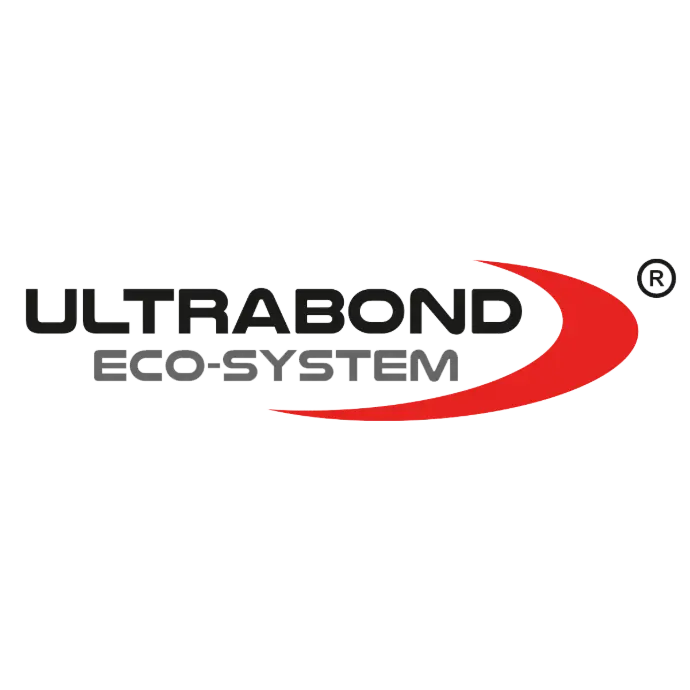
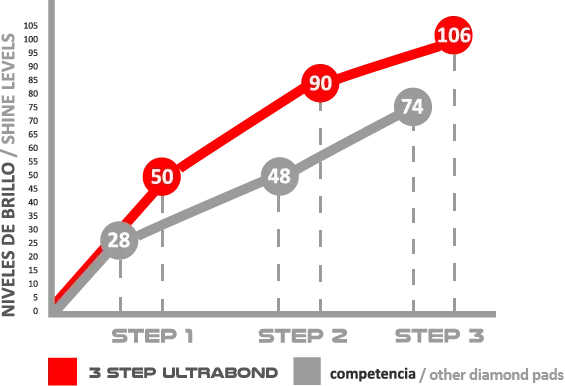
It allows the exact dispersion and positioning of diamond grains on the outside of an open-structured net-type support.
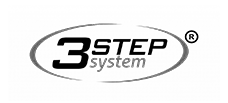
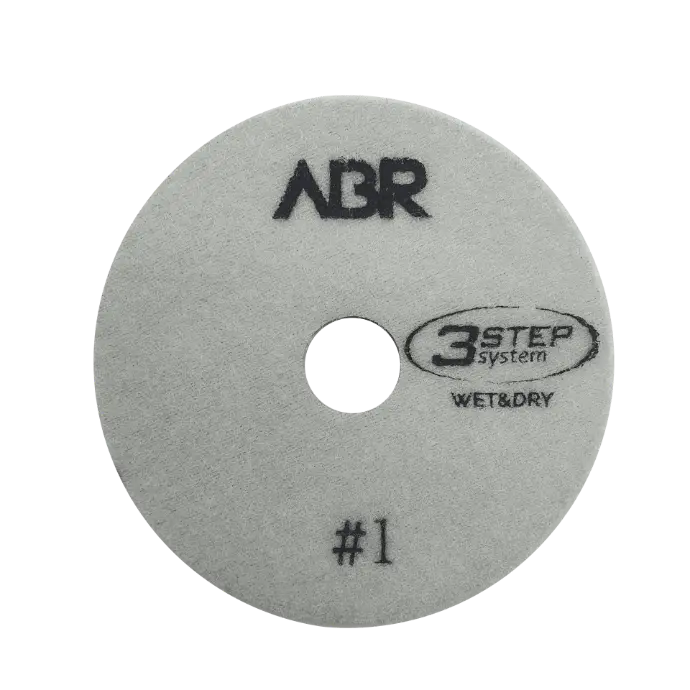
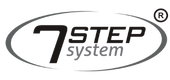
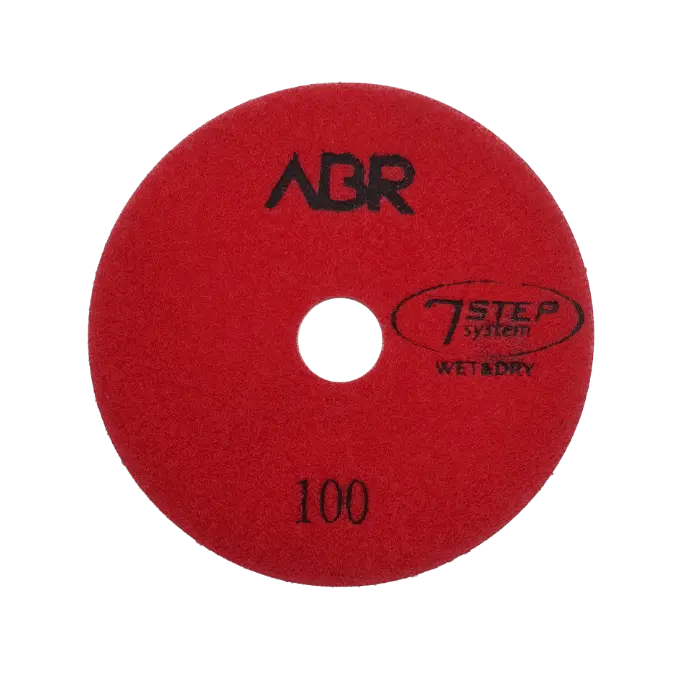
Revolutionary diamond polishing system in seven steps. Time reduction and cost savings compared to the use of traditional abrasives in the polishing and brightening of surfaces.
Revolutionary polishing system in only three steps. Reduces unnecessary steps to achieve the desired level of polish and shine, saving tool costs and labour time.
Structured abrasives 100% effective right from the start. The linear micro-structure defined on the top of the product enables perfect work right from the start, without the need to prepare or open the tool beforehand.
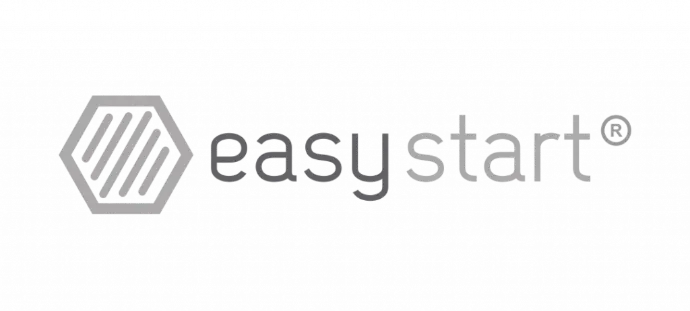
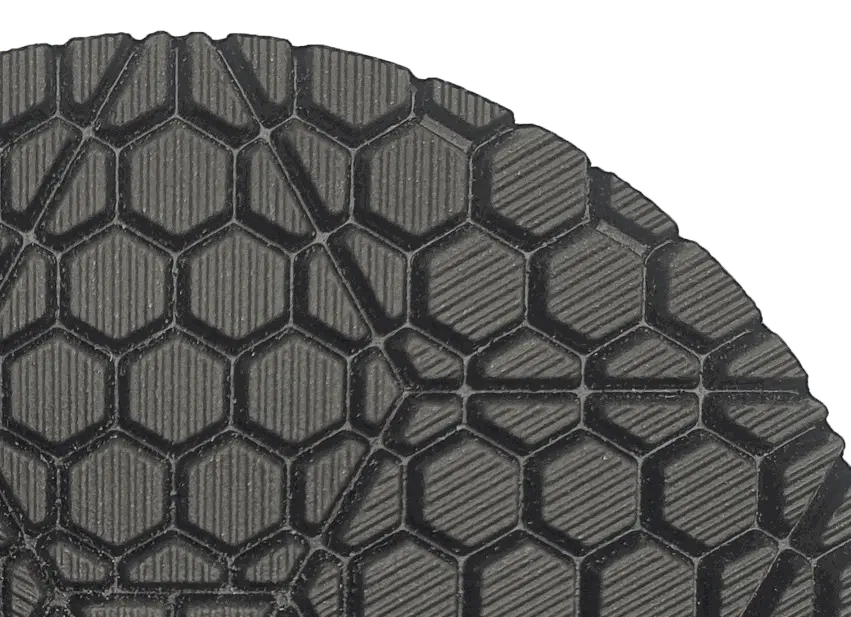
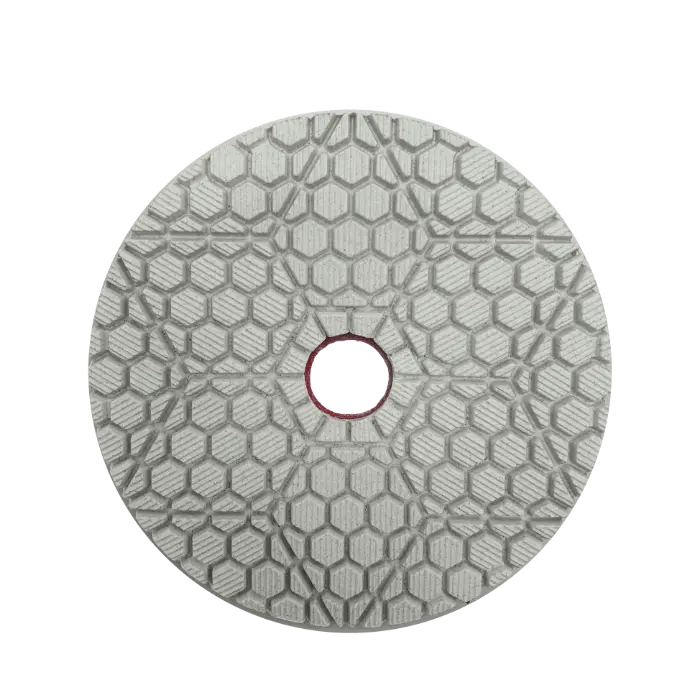
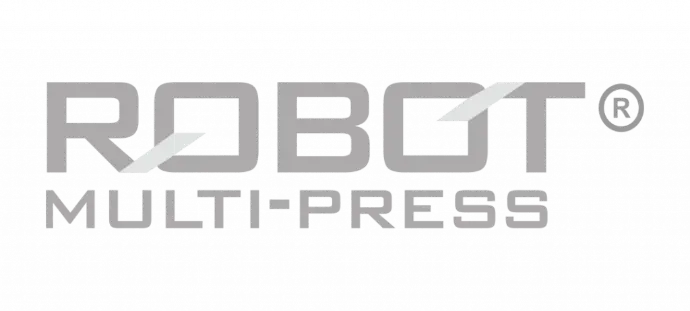
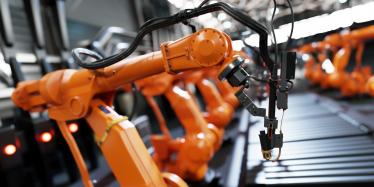
Example of maximum industrial automation by means of a multi-pressing system executed by robotic arms. This ensures maximum precision in processes and products, with the consistent quality that sets us apart.
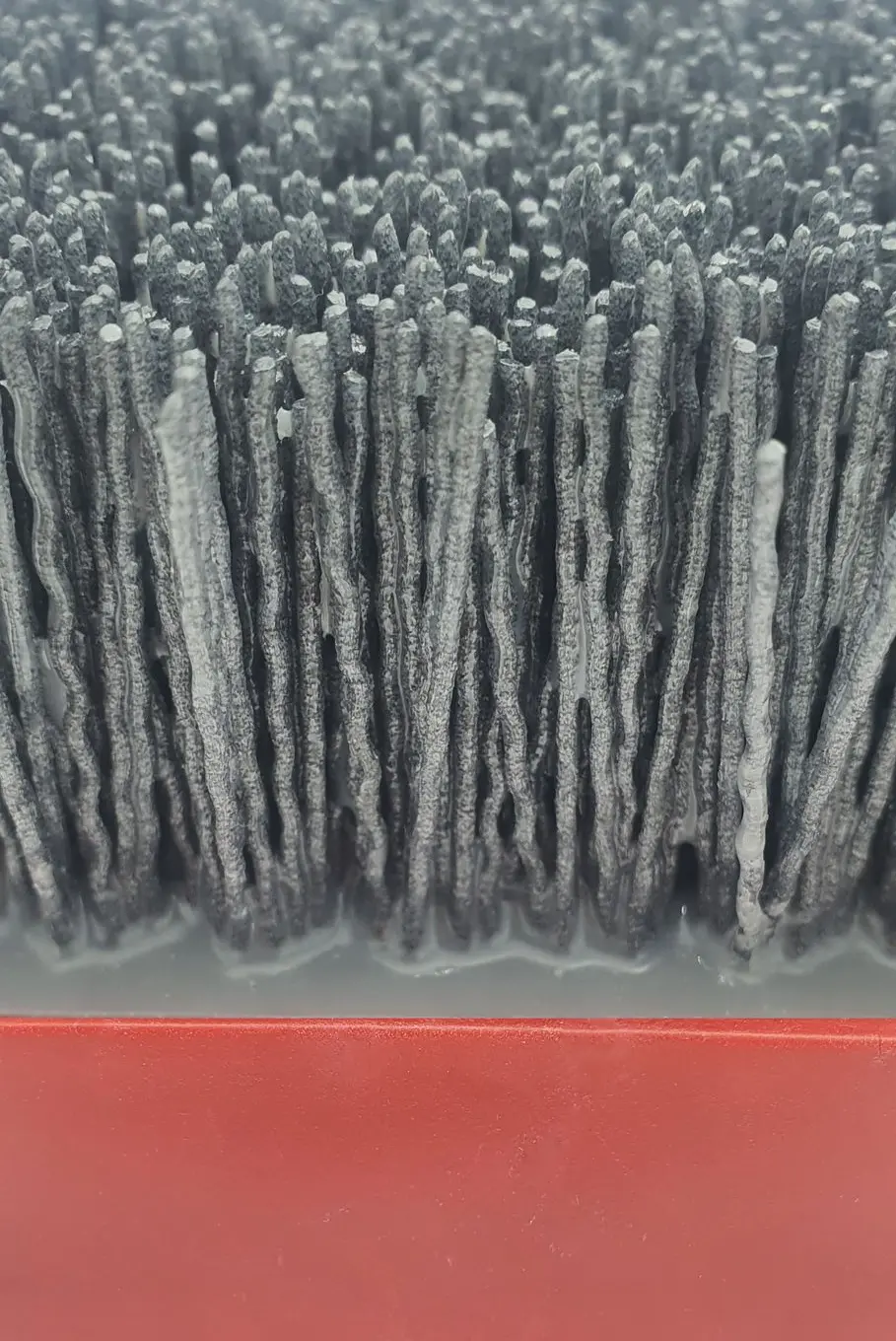
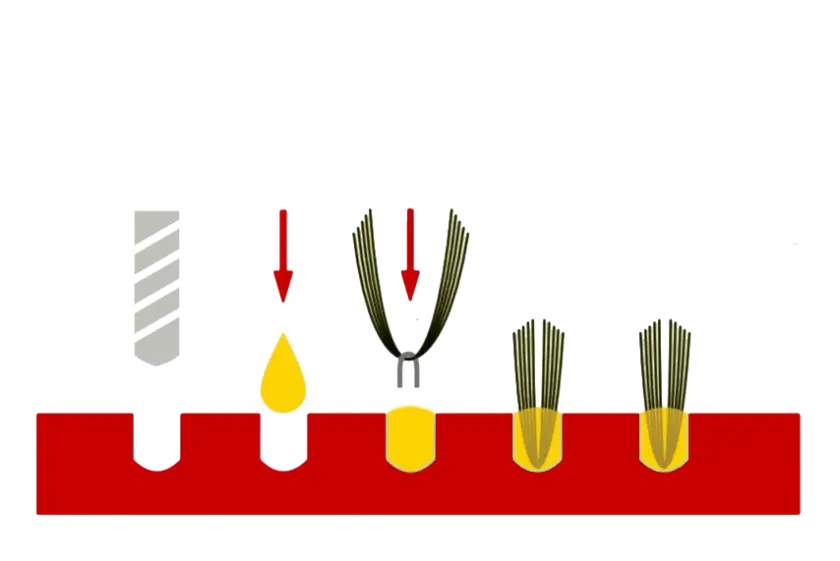
The most delicate surface that require the best finish, require very soft abrasive
products. RESIN formulations combine and elaborate selection of minerals,
bonded with specific synthetic resins, wich together with a controlled
production process, guarantee the best finish with maximum performance.
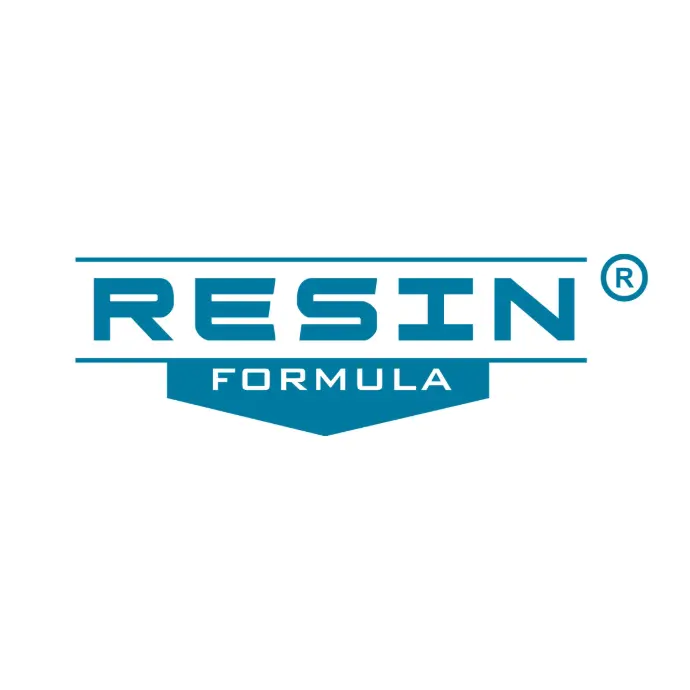
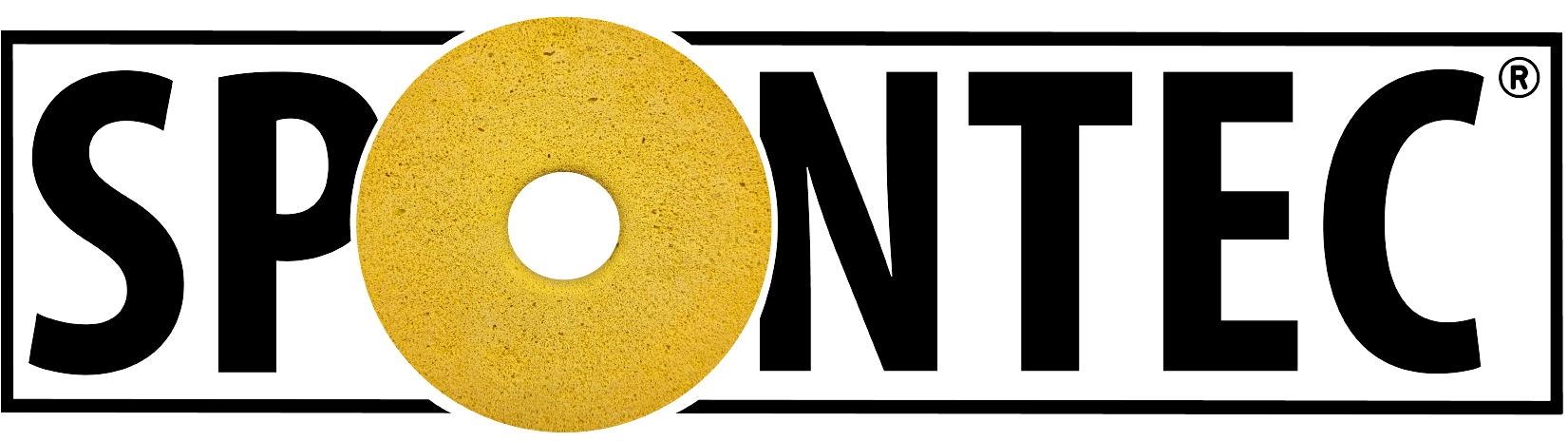
Technical sponge with diamond structure. A flexible exoskeleton with pores and internal channels that fully cool the diamond particles.
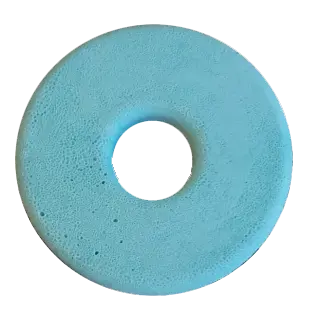
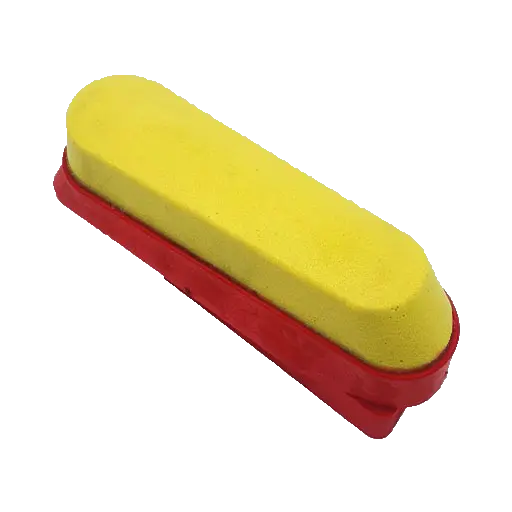
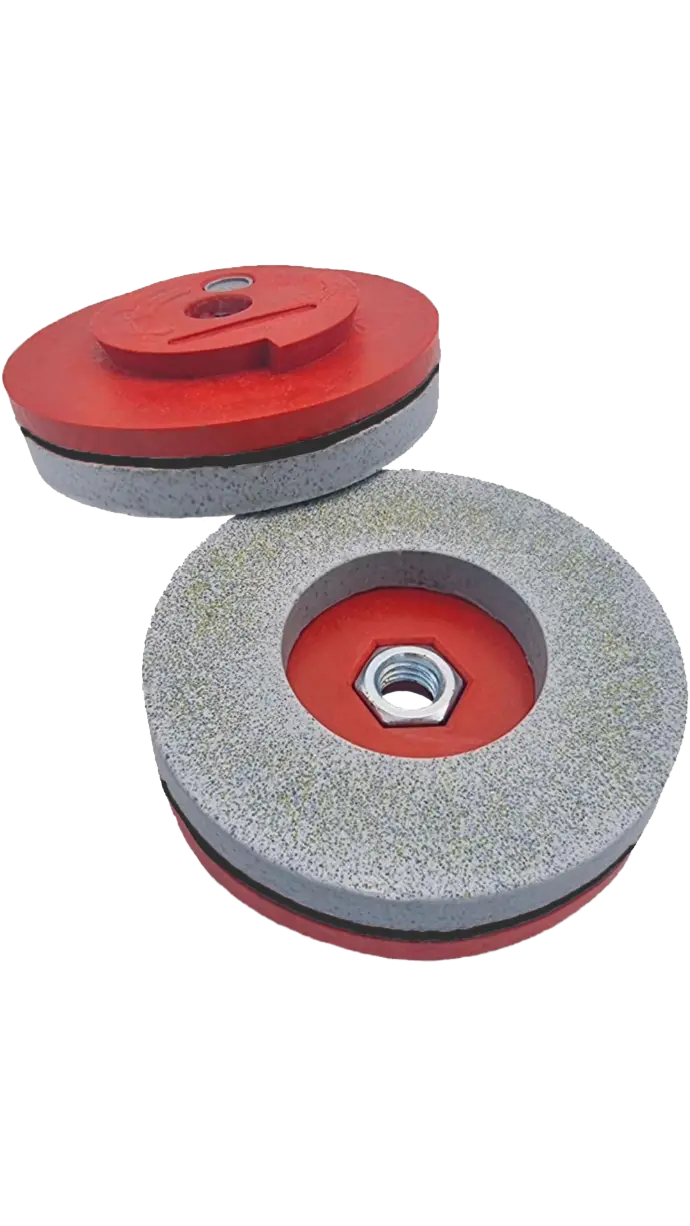
The Turbo design adjusts the pressure exerted on the abrasive, distributing it evenly to ensure controlled and uniform wear across the entire work surface. They are designed to operate at high speeds (typically between 3,000 and 5,000 RPM), allowing for fast grinding and polishing, reducing the working time required to achieve a professional finish.
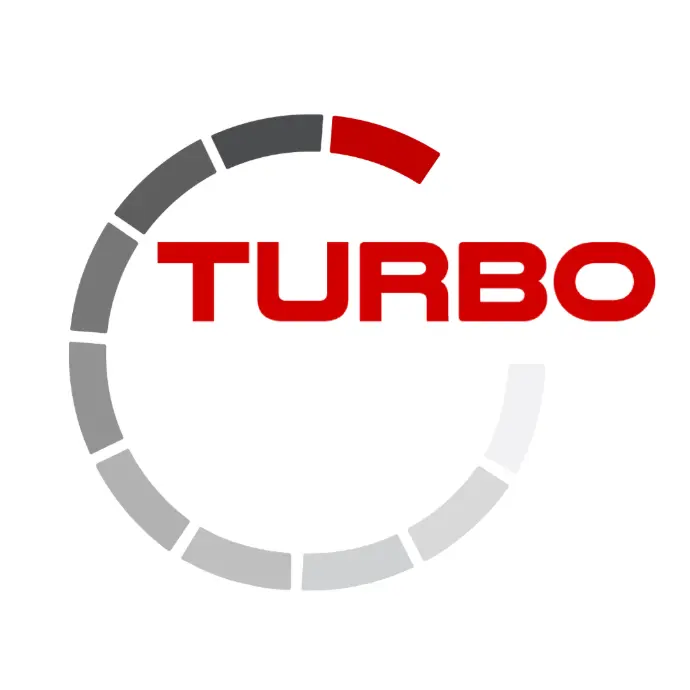